MULTI-SOLUTION BRIEFING 2025
Lean Asset Strategy and Mazda Monozukuri Innovation 2.0:
Under the 2030 Management Policy, Mazda defines the years leading up to 2030 as the Dawn of Electrification. For these years, Mazda strives to cater to diversifying customer needs, wants, and lifestyle by offering “Multi-Solution” for electrification, with the aim of striking the right balance of effective carbon neutrality and robust business growth.
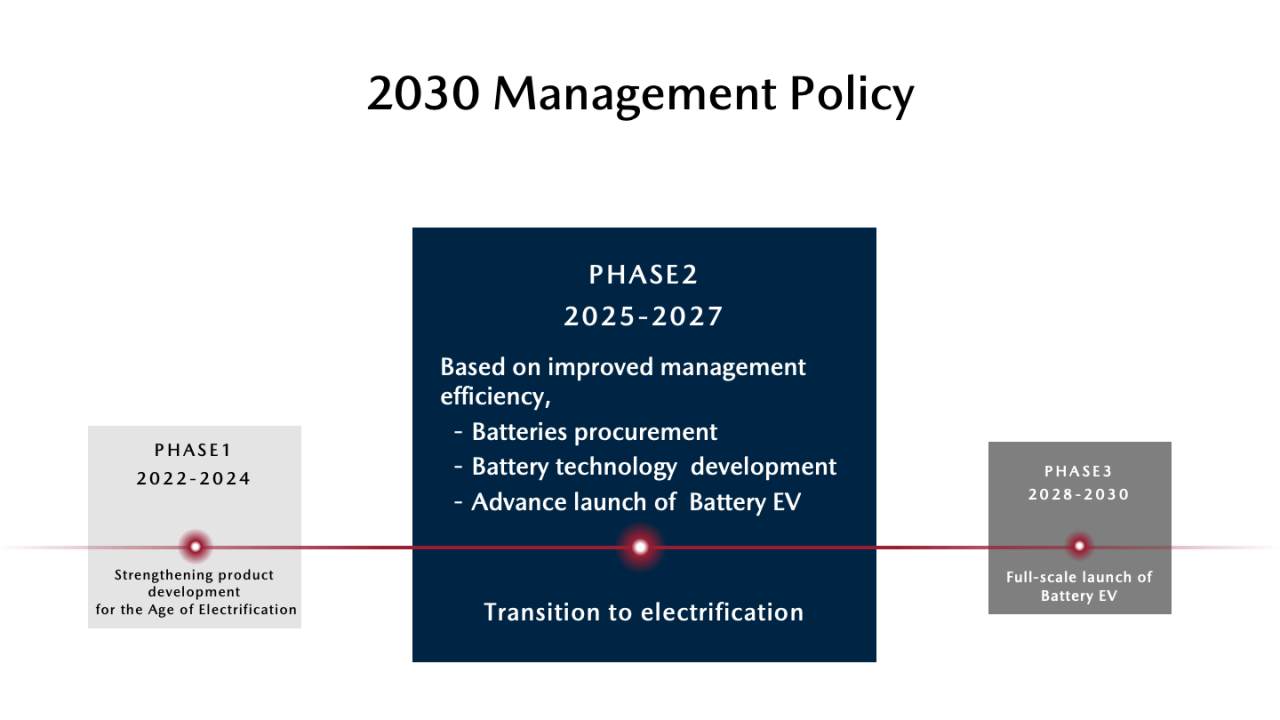
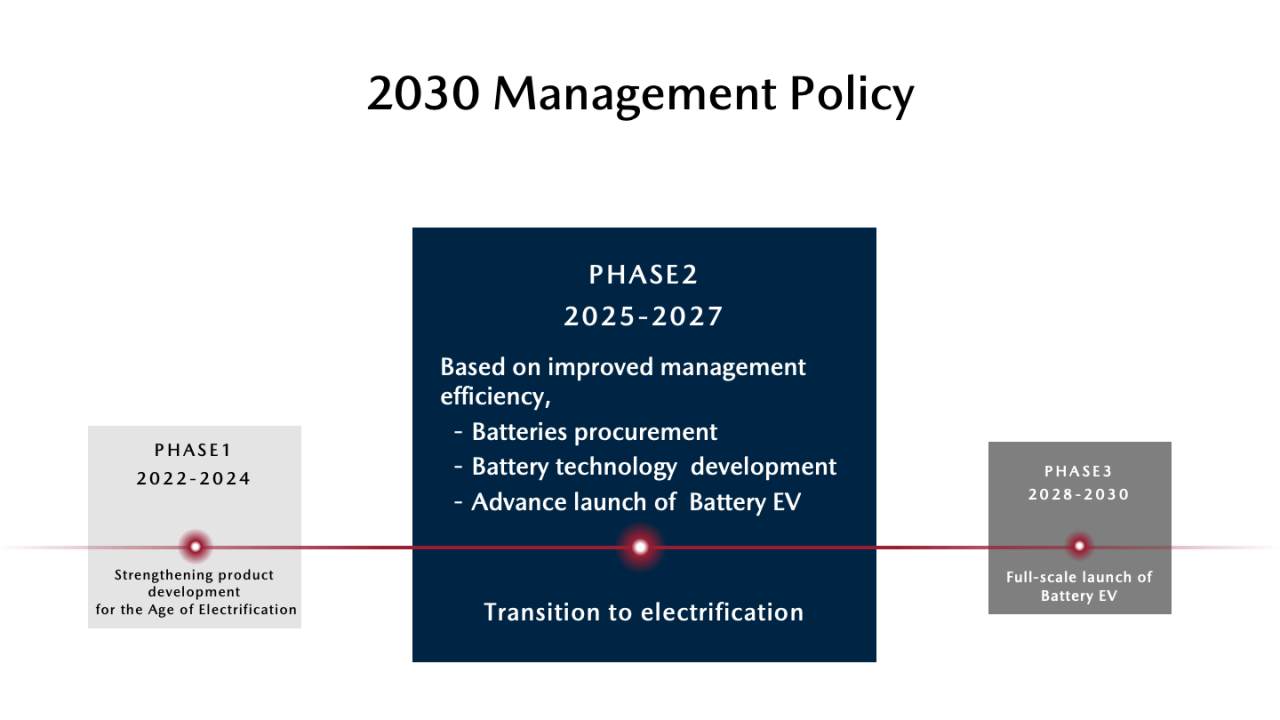
LEAN ASSET STRATEGY
Lean Asset Strategy is an implementation strategy that is unique to Mazda, a niche player in the industry, to better utilize its available assets for launching diverse products, in different sizes and types, and electrification technologies to the market in a timely manner, which ultimately leads to enhanced corporate value.
1.5 trillion yen electrification investment until 2030, announced in November 2022, is estimated to remain the same in spite of 2 trillion yen forecast reflecting the impact of inflation. The saving will be achieved by battery investment optimization and other efficiency measures. 750 billion yen battery investment, which assumed in-house procurement of all batteries and reflecting inflation, is expected to be reduced by 50% thanks to collaboration with partners.
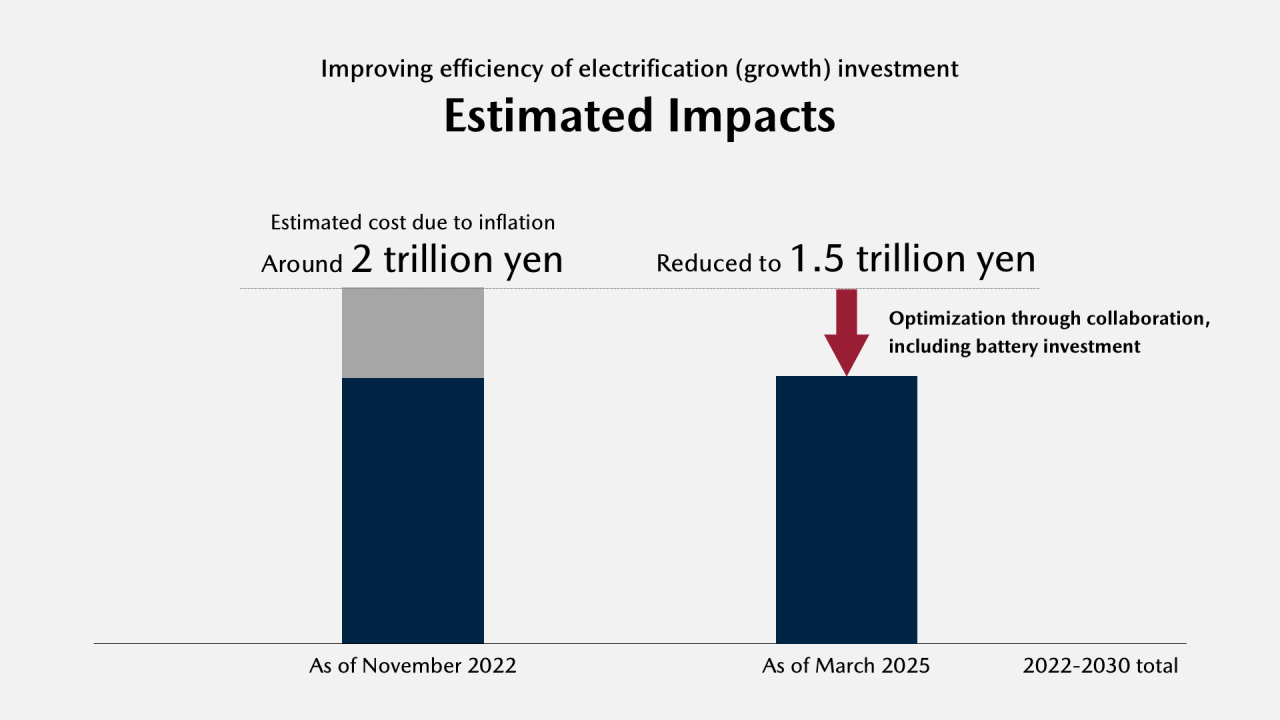
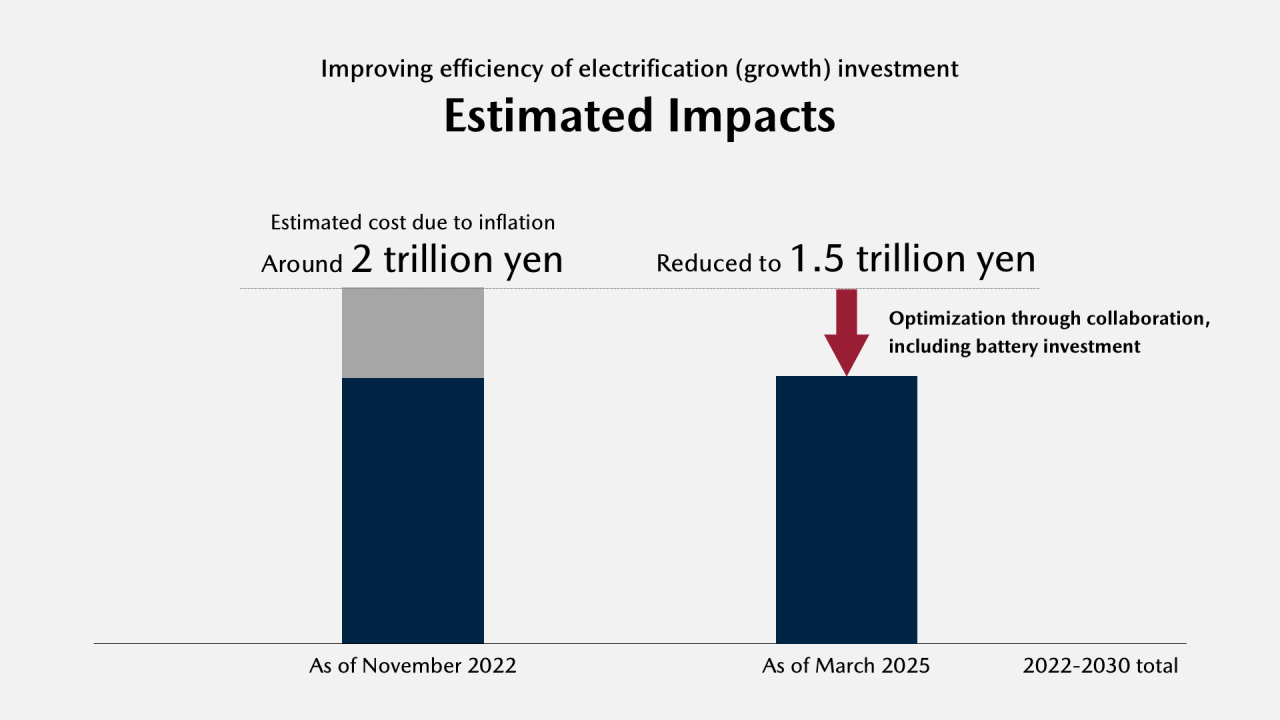
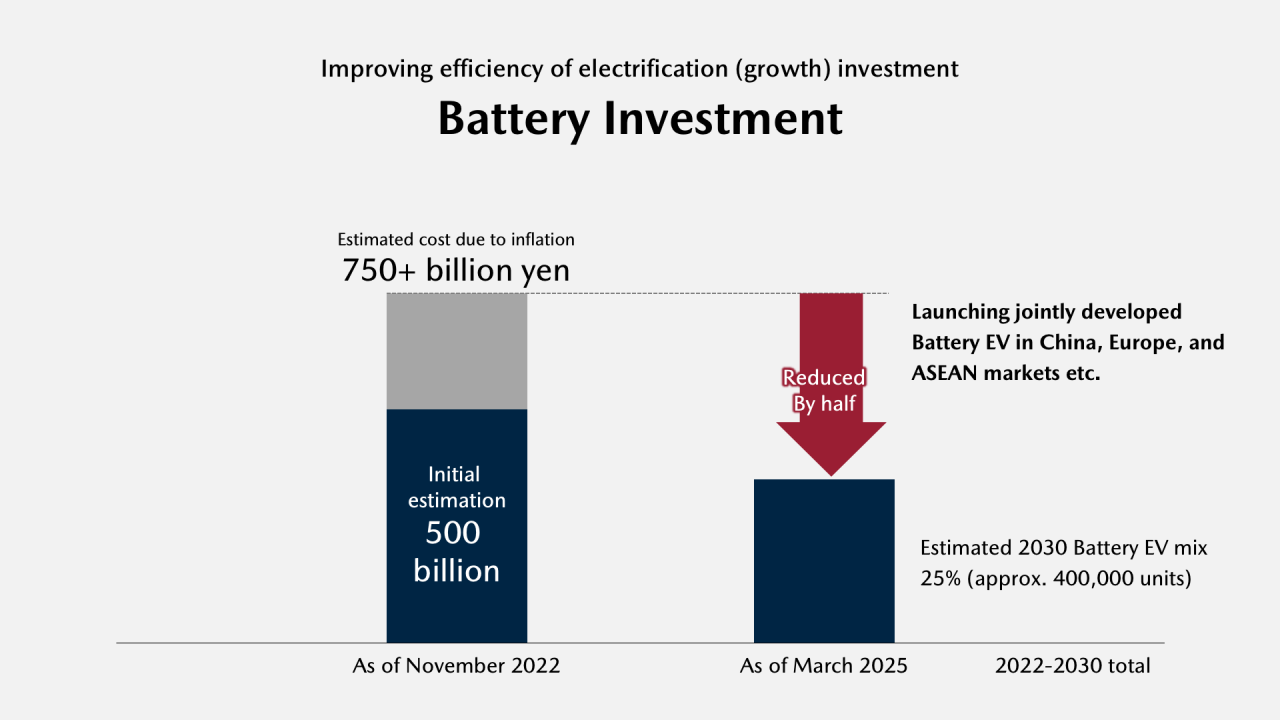
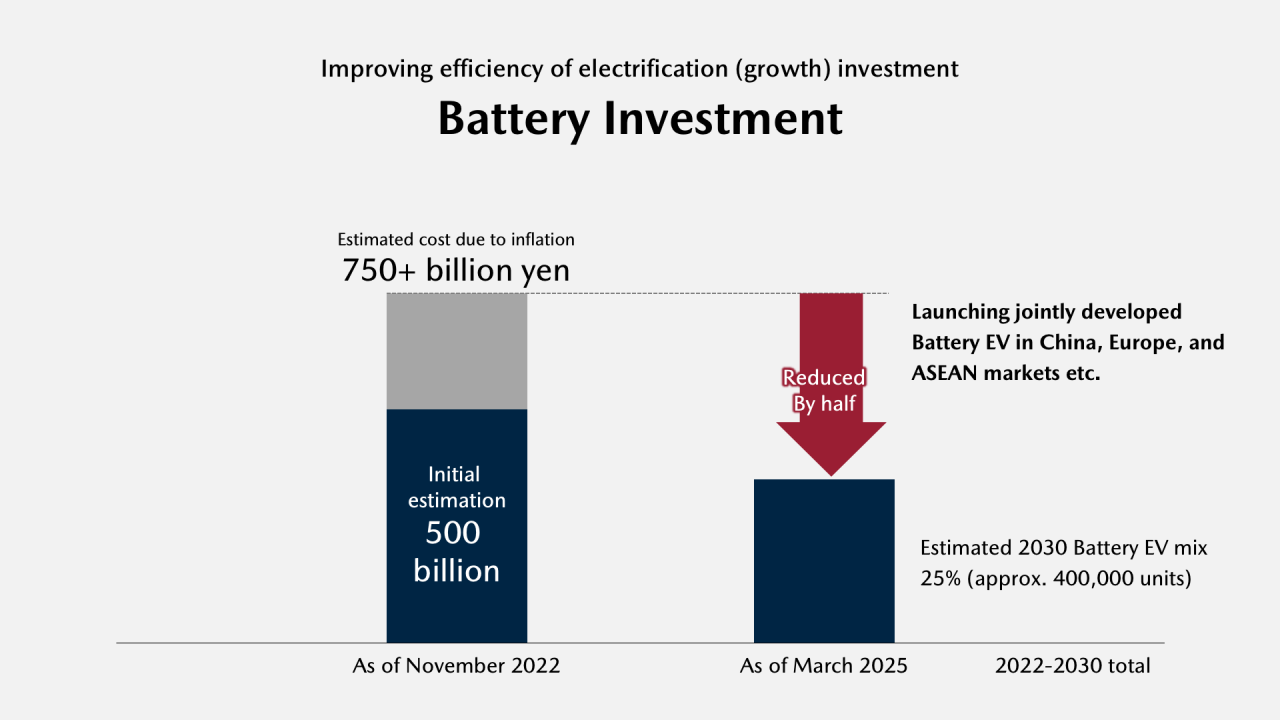
In addition to the collaboration announced in 2022 to develop a production hub for electrification units in Hiroshima, our home town, we are working on the development of electrification technologies by leveraging the partnership.
We are working with alliance partners such as Toyota, DENSO and BluE Nexus on electric/electronic architecture, advanced driving assistance system, electric powertrain and so on to develop these technologies efficiently.
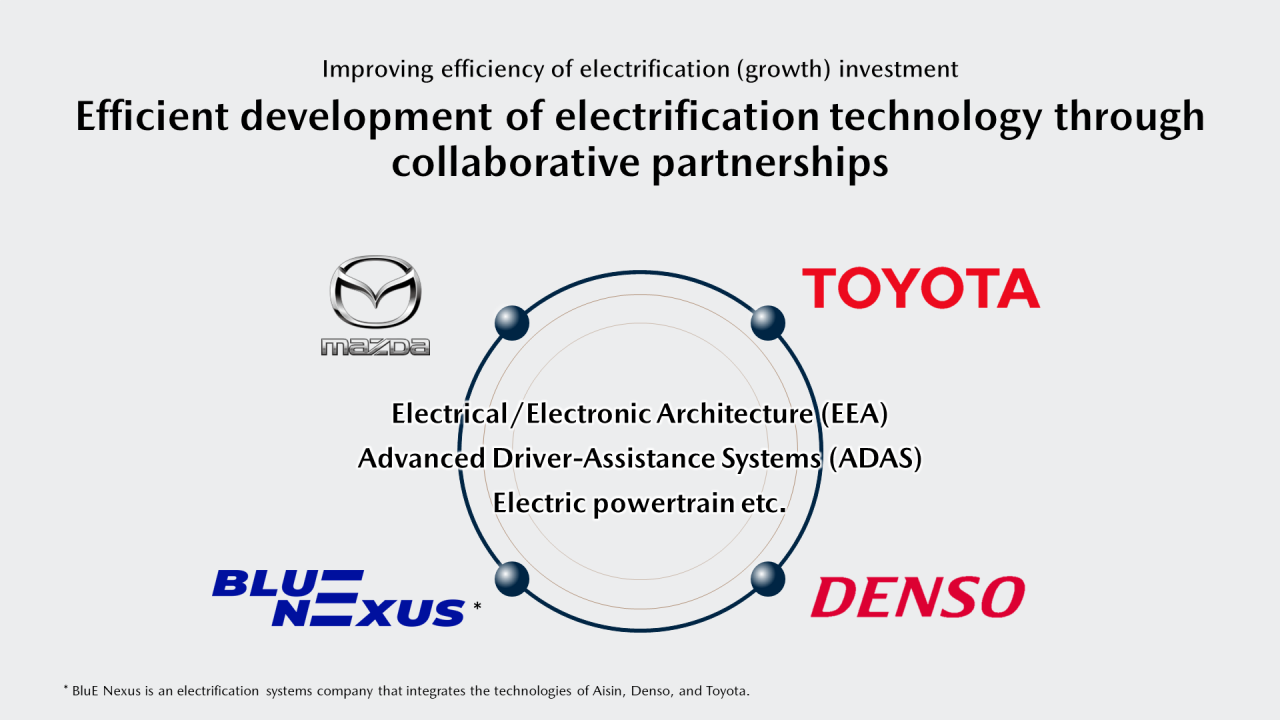
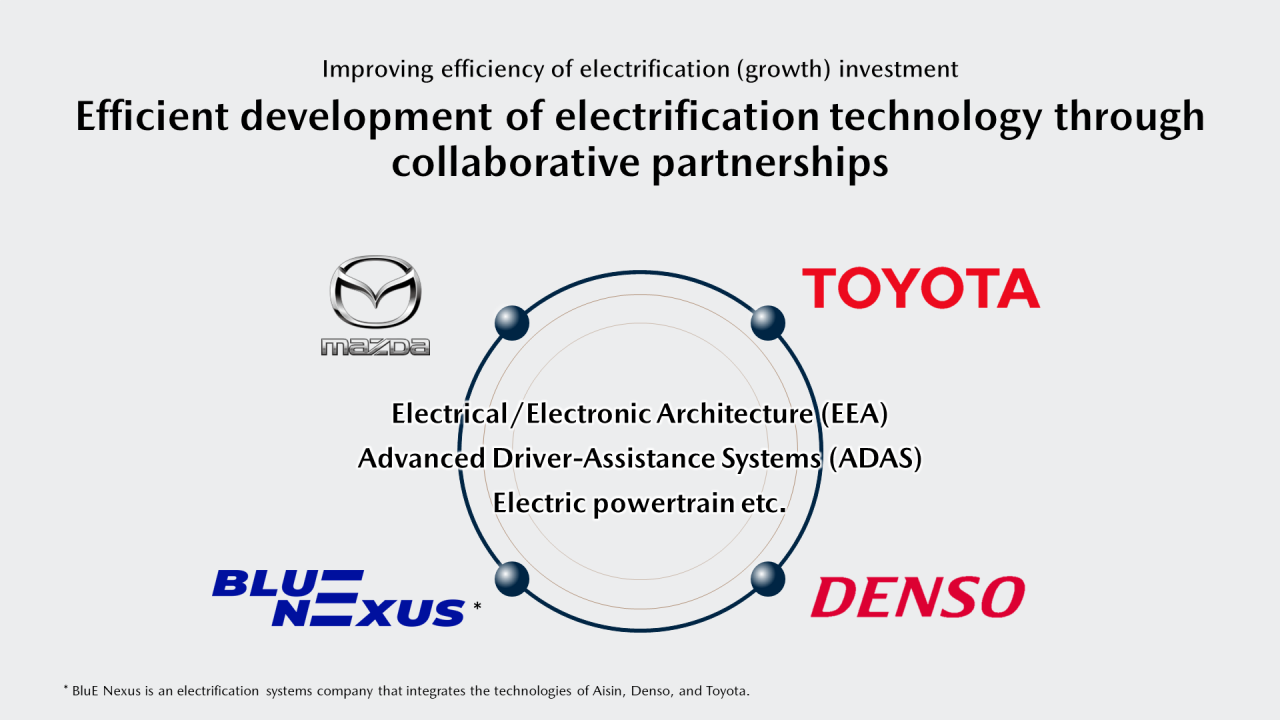
MAZDA MONOZUKURI INNOVATION 2.0
In manufacturing, Mazda is currently implementing its unique development and production processes innovation called Mazda Monozukuri Innovation 2.0. In development, assets that are more than 3 times of Monozukuri Innovation 1.0 are acquired without increasing resource and time. In other words, Mazda has successfully achieved a threefold increase of development productivity.
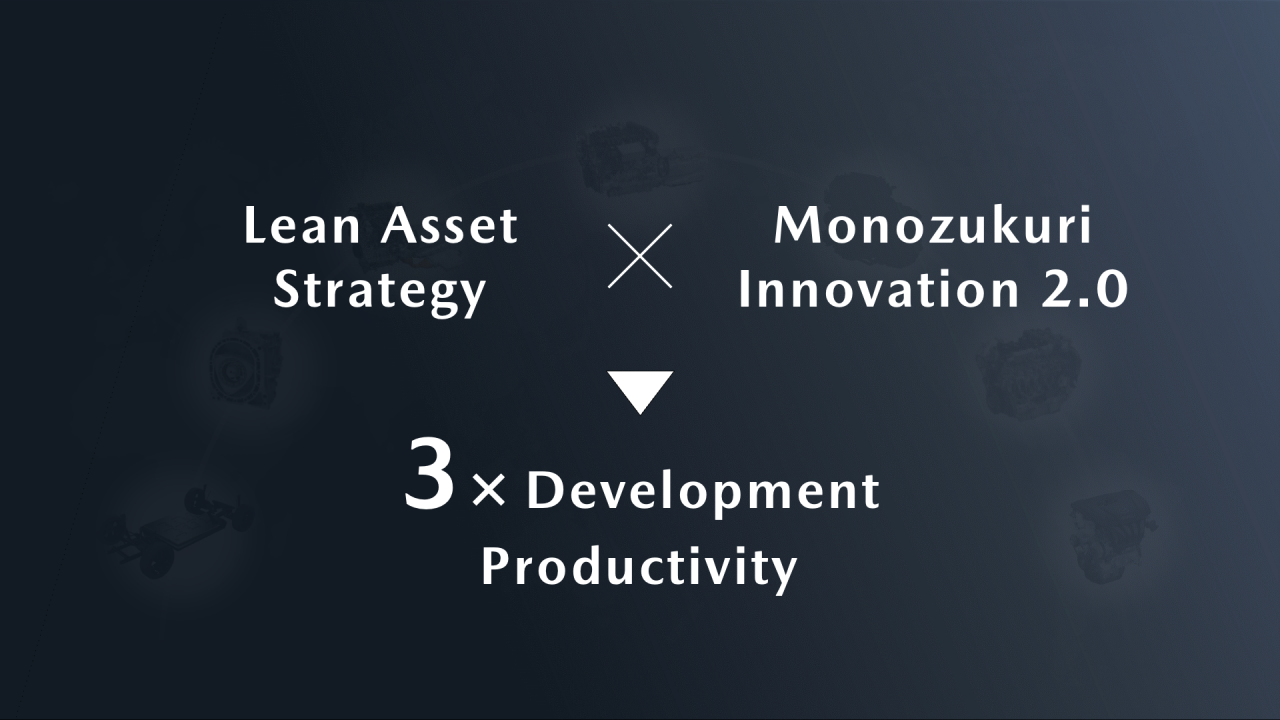
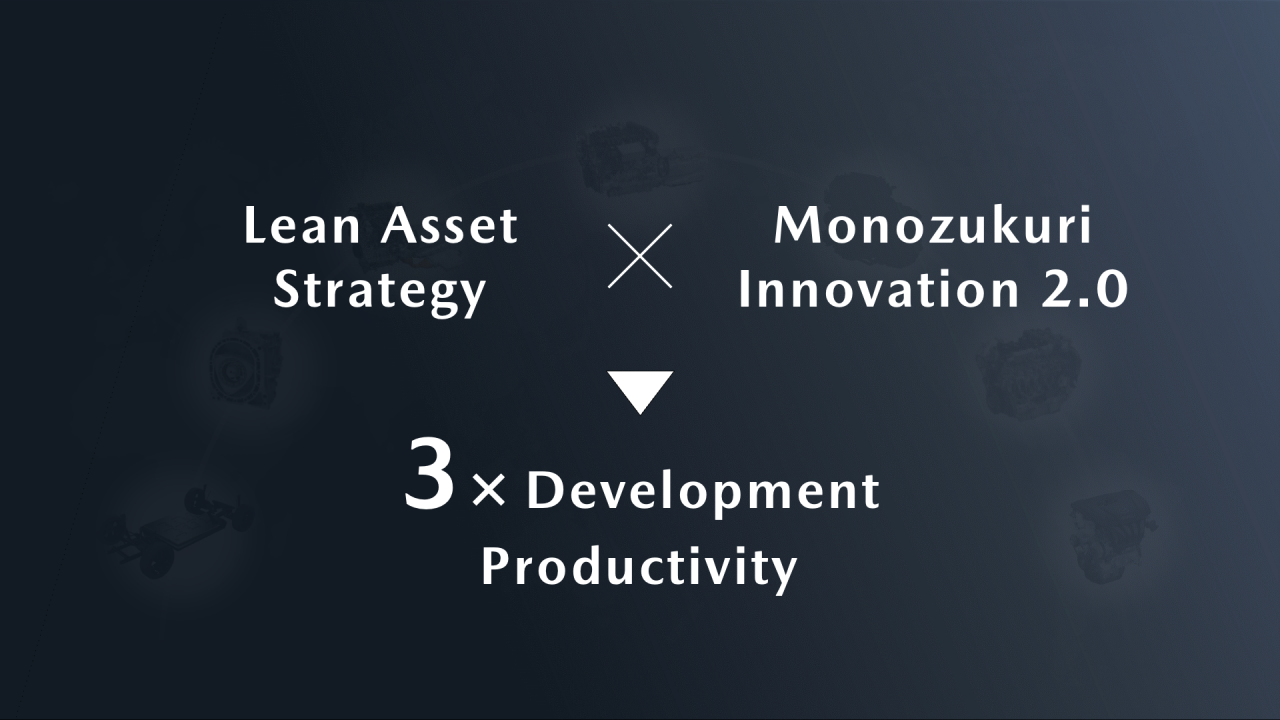
Regarding Mazda’s Batter EV developed in-house, planned for launch in 2027, evolution of model-based development (more on this later) and collaborative product development with partners are likely to reduce development investment by 40% against conventional development process, and development workload by 50%.
Looking at production processes, mixed production of Battery EV and ICE models, achieved by using our available assets, allows Mazda to produce Battery EV without constructing a dedicated plant. Compared to constructing a new Battery EV-dedicated plant, initial facility investments are expected to be reduced by 85%, and production preparation period will be shortened by 80%.
Mazda is committed to achieving sustainable growth by securing high asset efficiency with smaller investments, offering competitive products and technologies, and generating positive ROI.
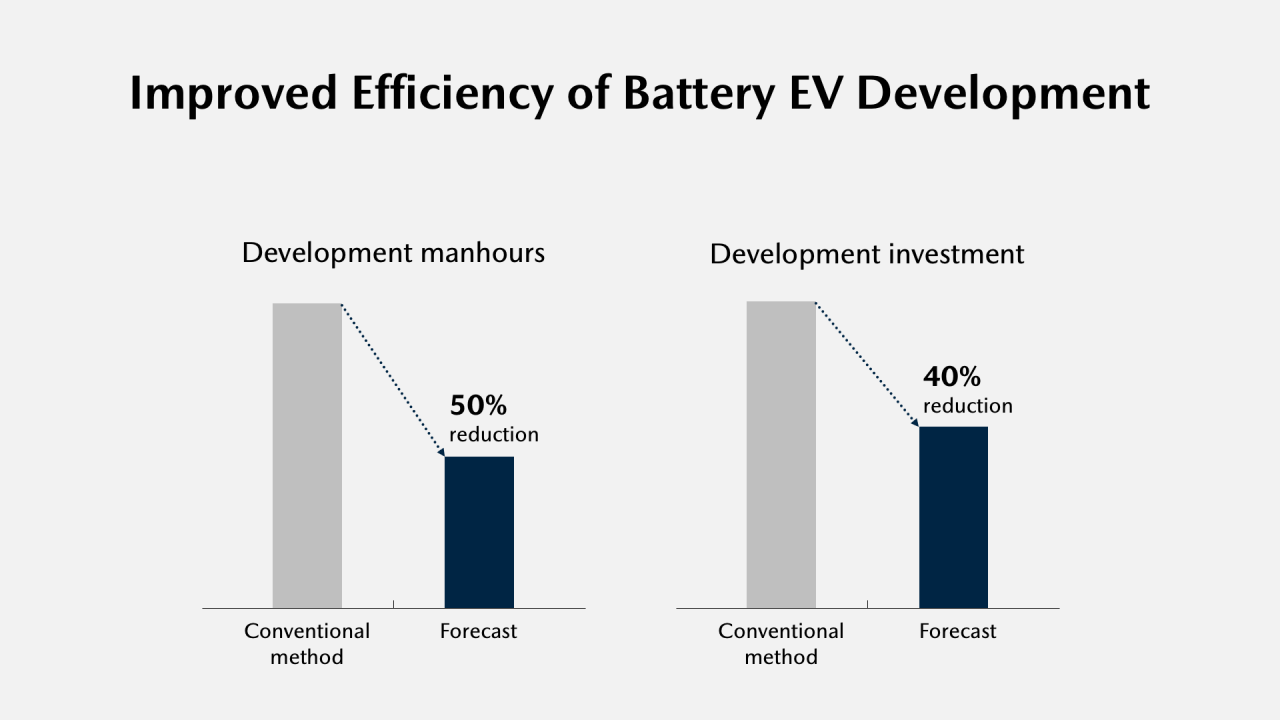
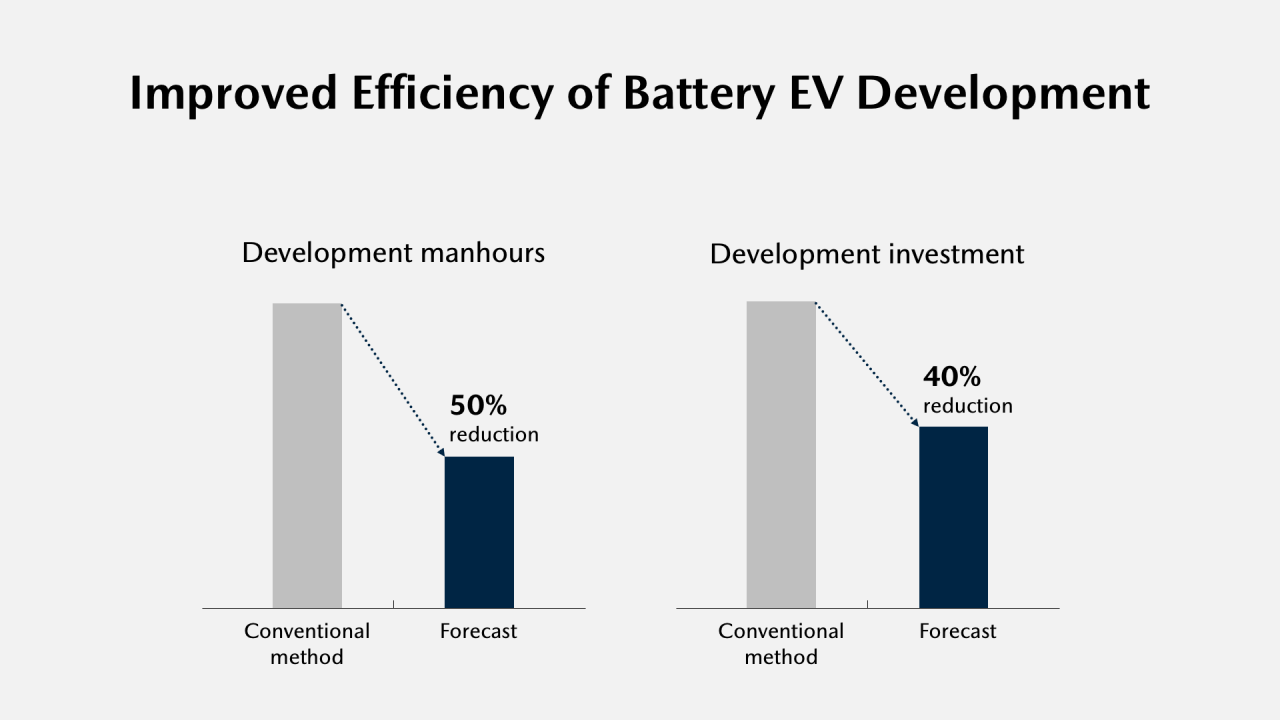
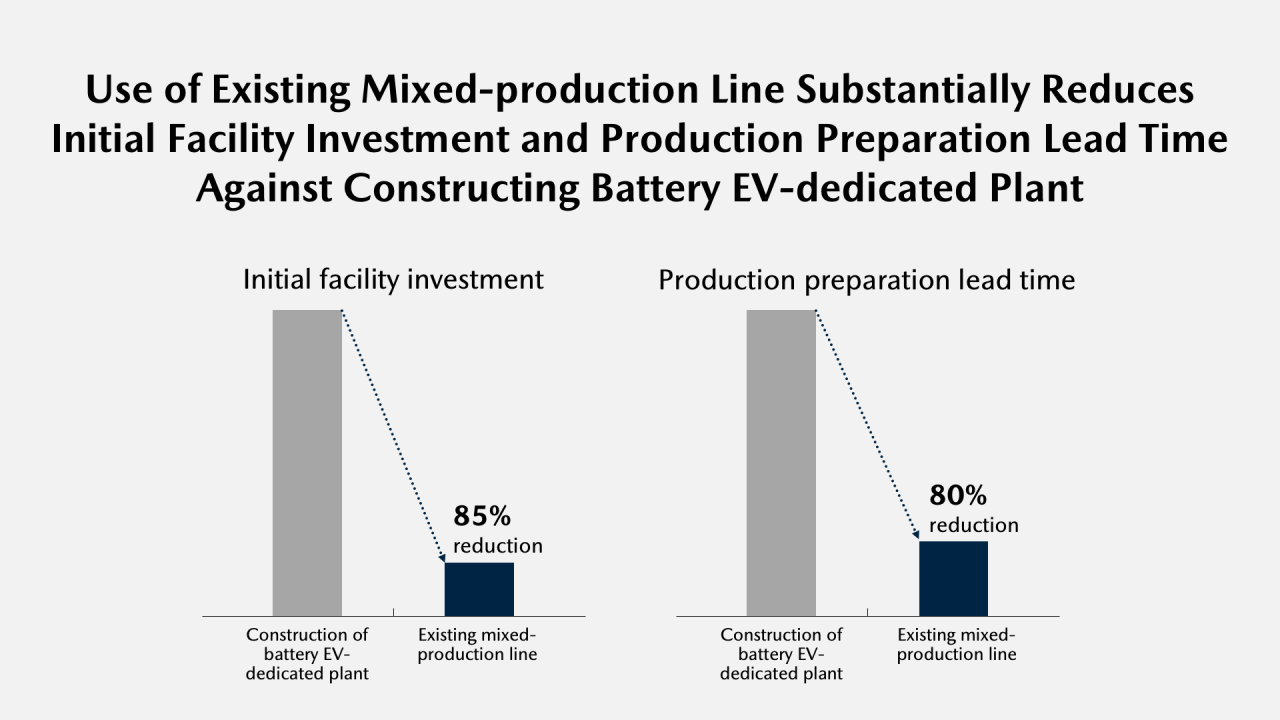
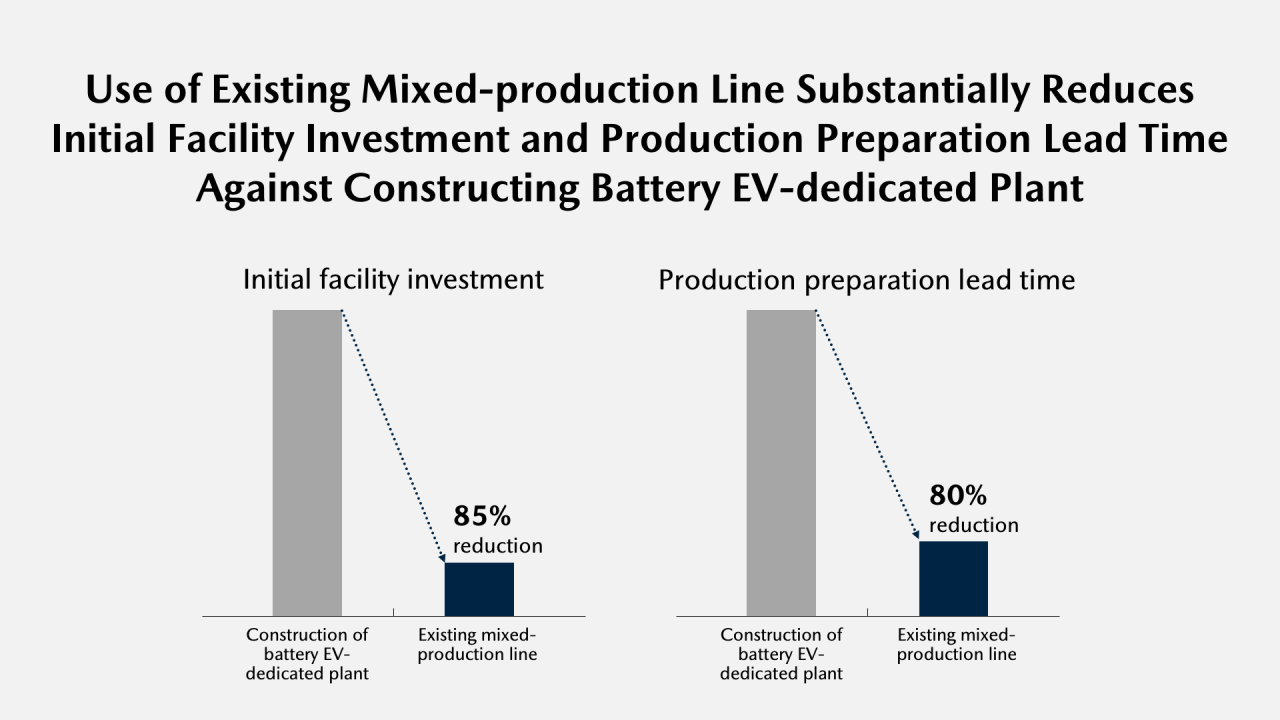
MAZDA MONOZUKURI INNOVATION 1.0 (2006-)
Monozukuri Innovation 1.0 is Mazda’s unique development and production processes innovation that can only come from a company of Mazda’s size, aimed at striking the right balance of flexibly catering to customer’s diverse needs and demand variations, and securing efficiency by economies of scale.
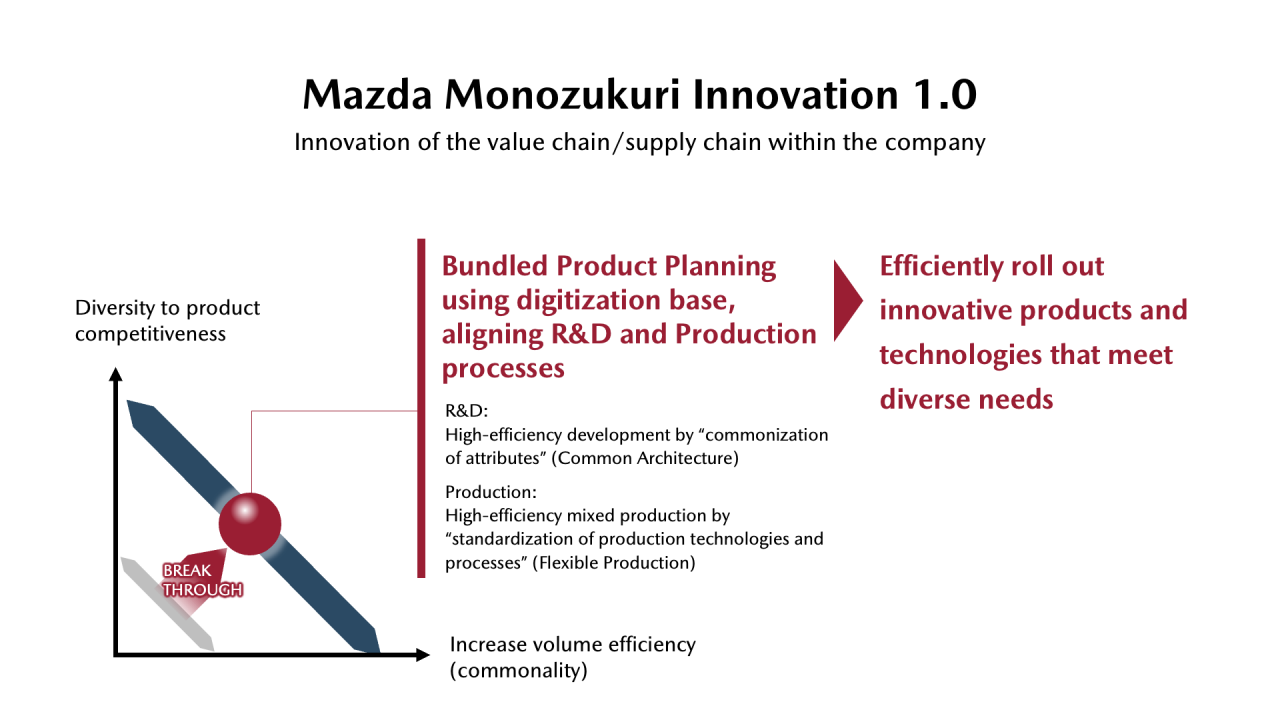
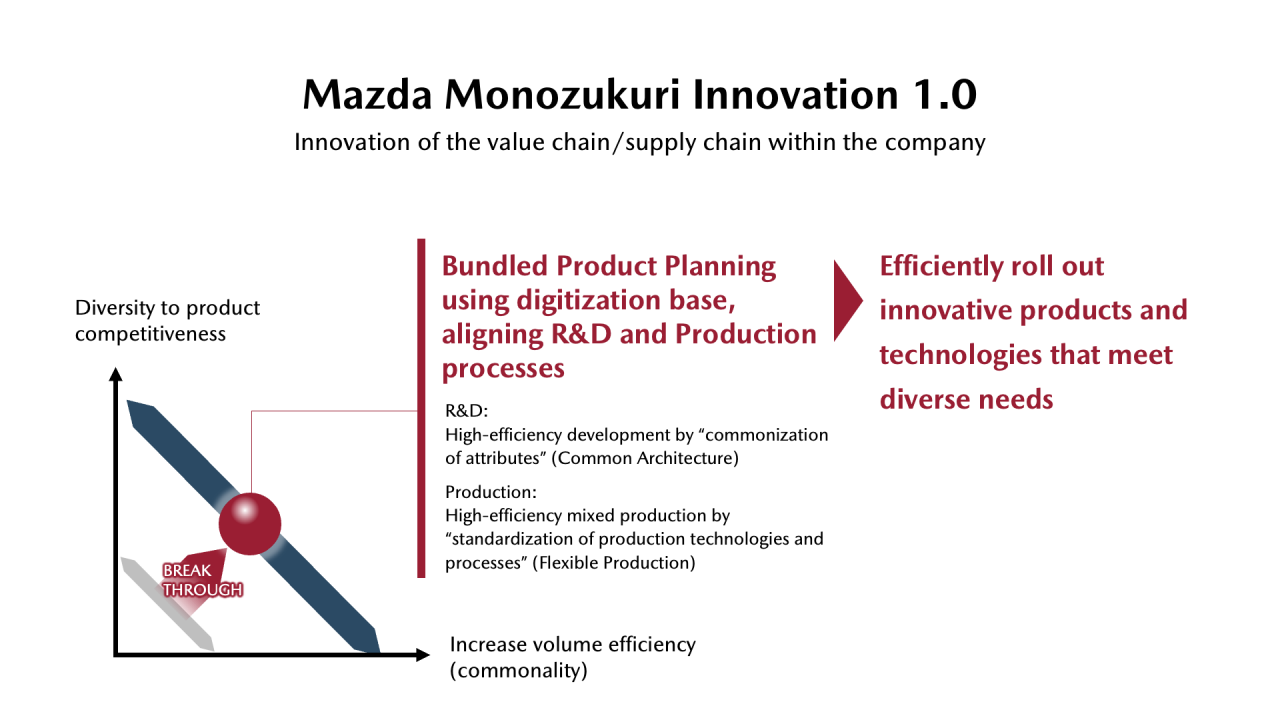
As with having been the first in Japan to introduce computers in production lines in 1960, Mazda started to embrace digitalization from an early stage. Since 1996, Mazda Digital Innovation activities have been implemented in which data previously managed separately by each department is centrally managed as 3D digital master data. As a result, the lead time from design freeze to mass production was almost halved by 2006.
Building upon this, under Monozukuri Innovation 1.0, products and technologies that would be needed in 5 to 10 years’ time are planned all together (bundled planning), and then the R&D and production departments work as one team to design standard structures (common architecture) and standard processes that can be used for a wide range of future products, after clarifying the fixed elements that can be shared across carlines and the variable elements that give each carline its own unique characteristics.
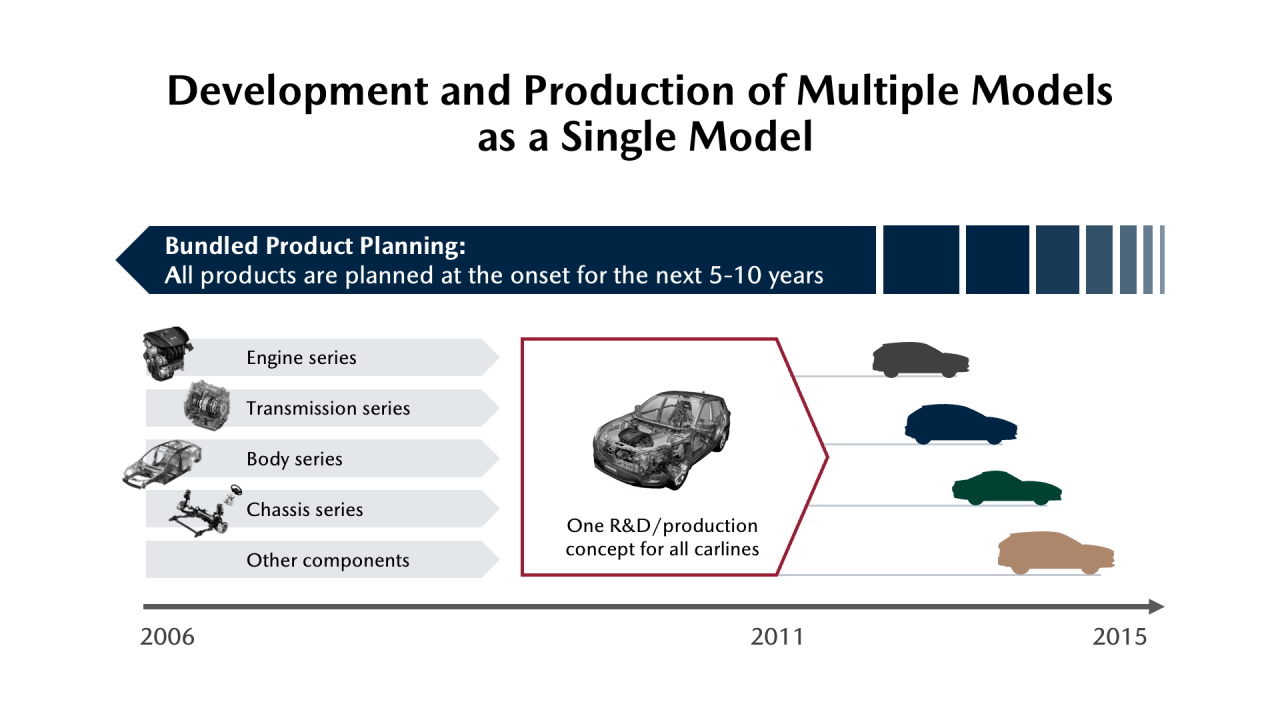
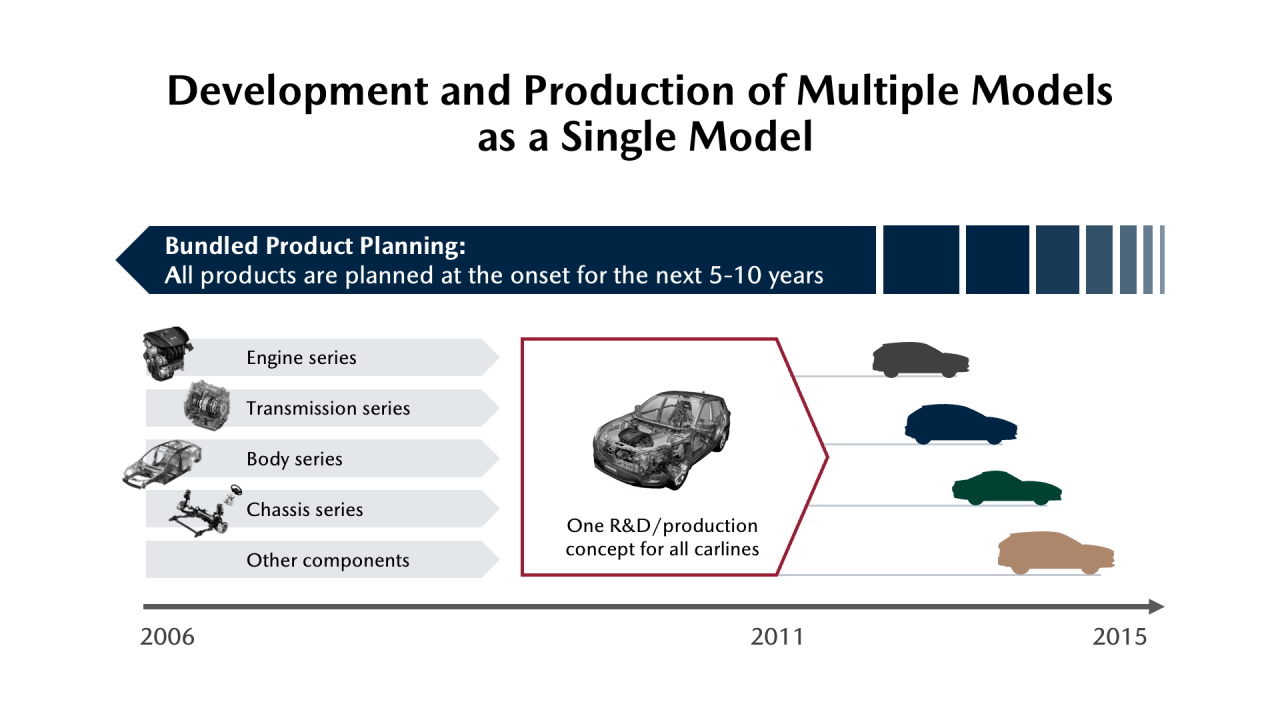
In development, characteristics, not hardware, were commonized. Taking the engine development as an example, commonization of combustion characteristics, or a combustion model, resulted in unification of the control software. This made it possible to shorten the development period of different engine displacements and their conformity to different markets, which is the most time-consuming part of engine development, by 50%.
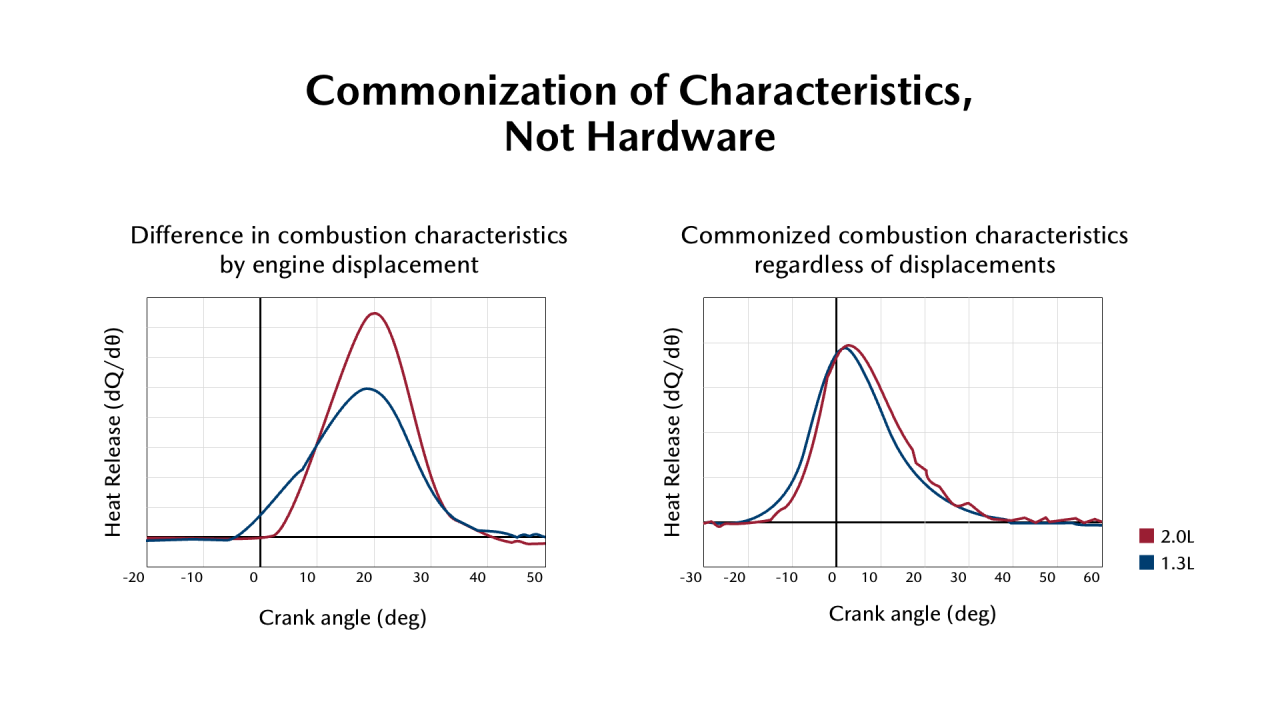
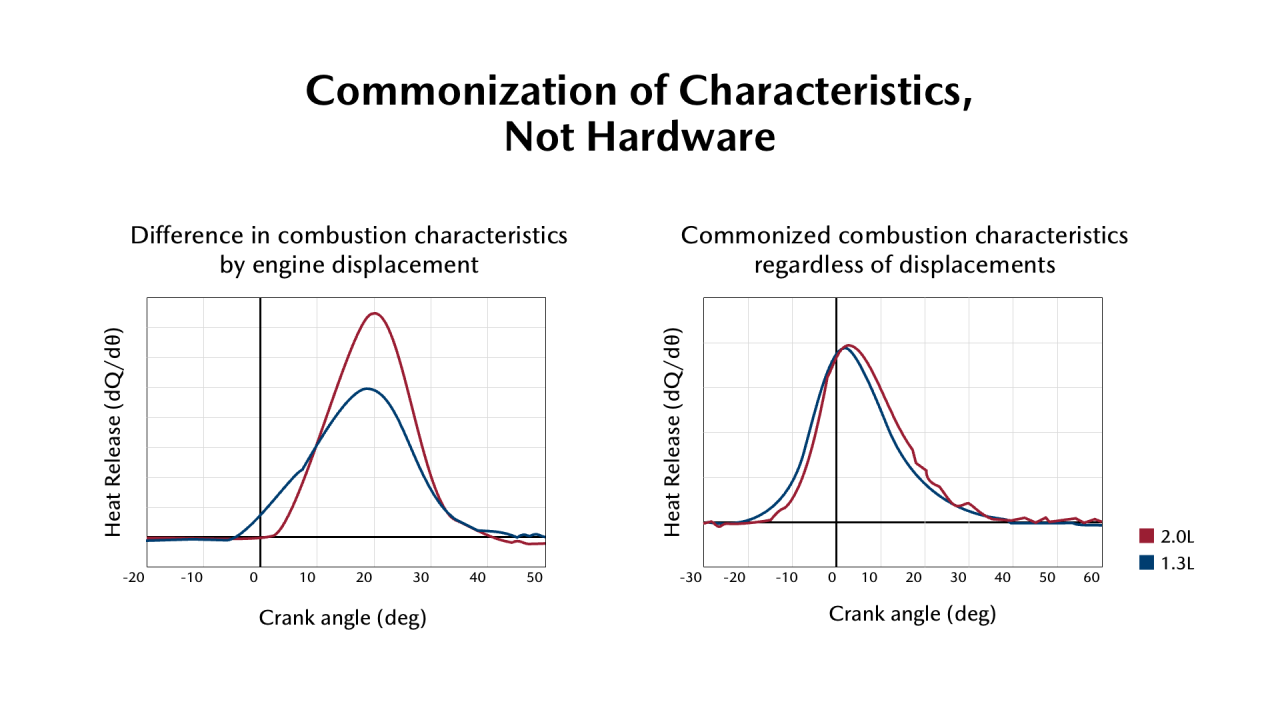
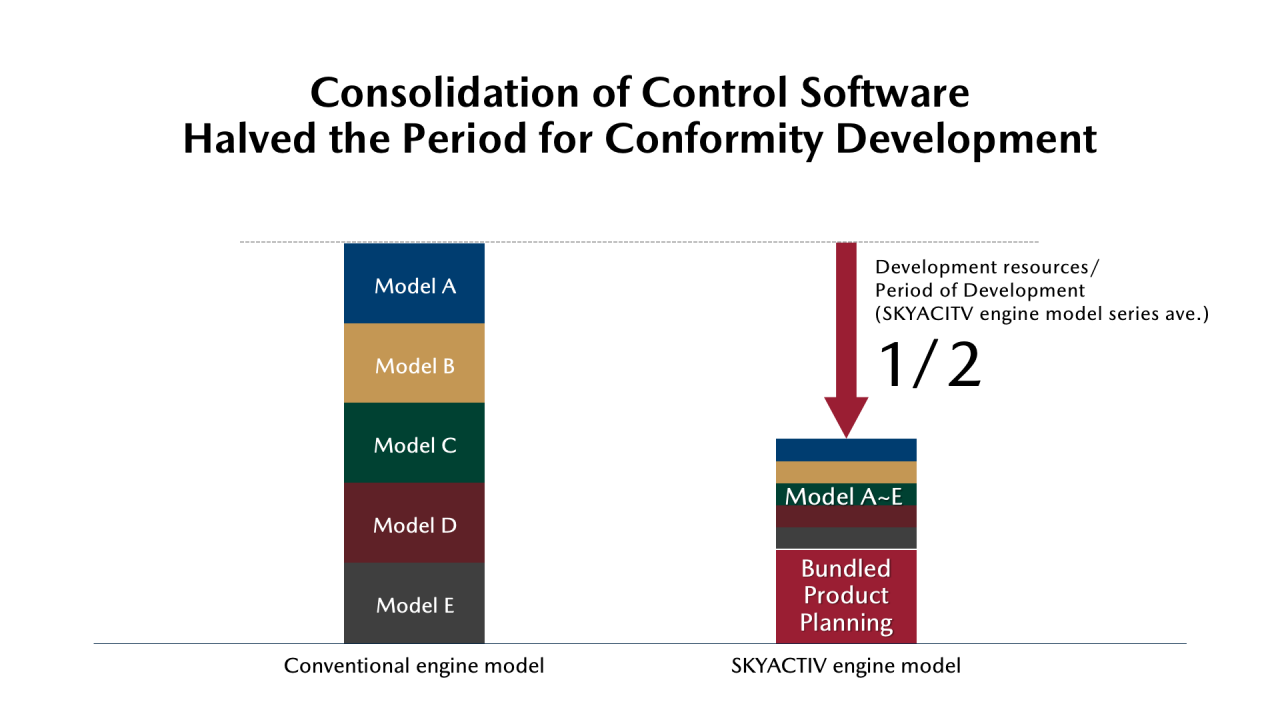
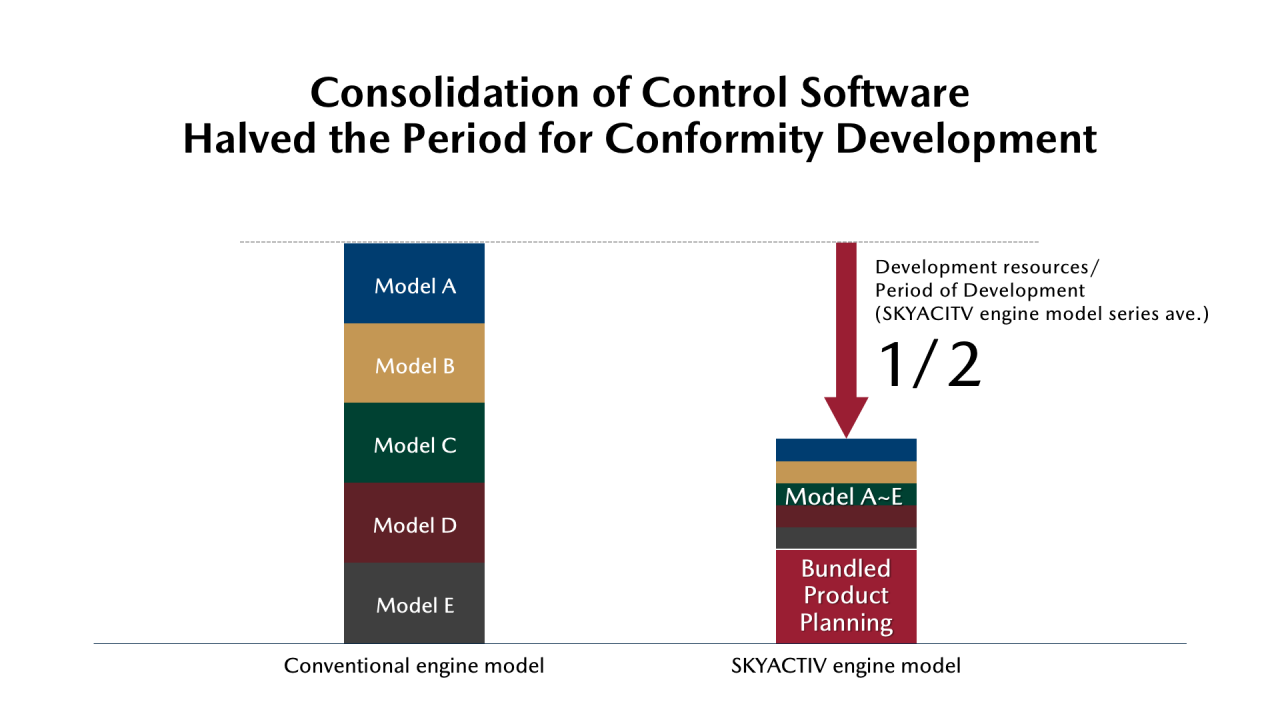
In manufacturing, highly efficient and flexible mixed production (flexible production) was established by Bundled Product Planning in advance. Model-unique operation procedures and processes were moduled in a sub line, a production line that bundles multiple components/parts, and installed in the main line. To keep the main line simple and short, the sub line was designed to flexibly accommodate fluctuating production volume. These actions worked to significantly improve flexibility of production line that is capable of maintaining high utilization rate.
MAZDA MONOZUKURI INNOVATION 2.0 (2015-)
In the age of electrification and intelligence technology, Monozukuri has become increasingly complex. In Monozukuri Innovation 2.0, Mazda, as a niche player, strives to further enhance flexibility and efficiency of R&D and production, and continue to pursue Bundled Product Planning from Battery EV to ICE models.
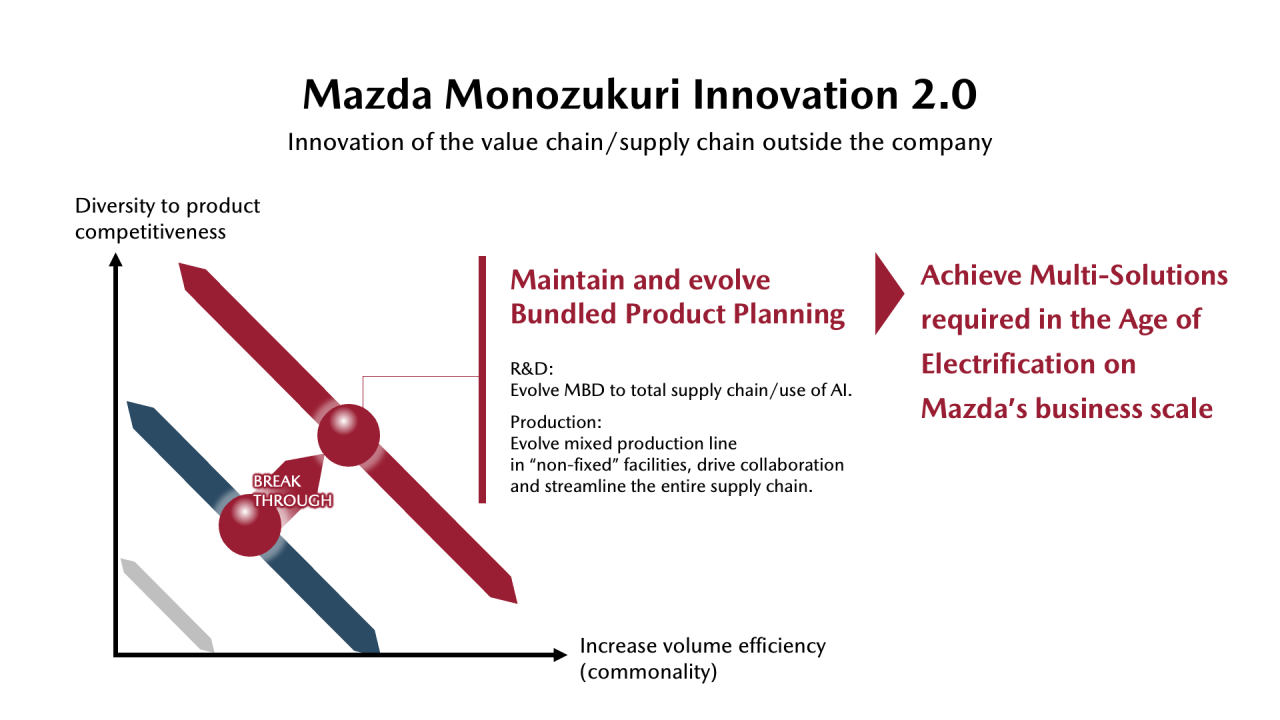
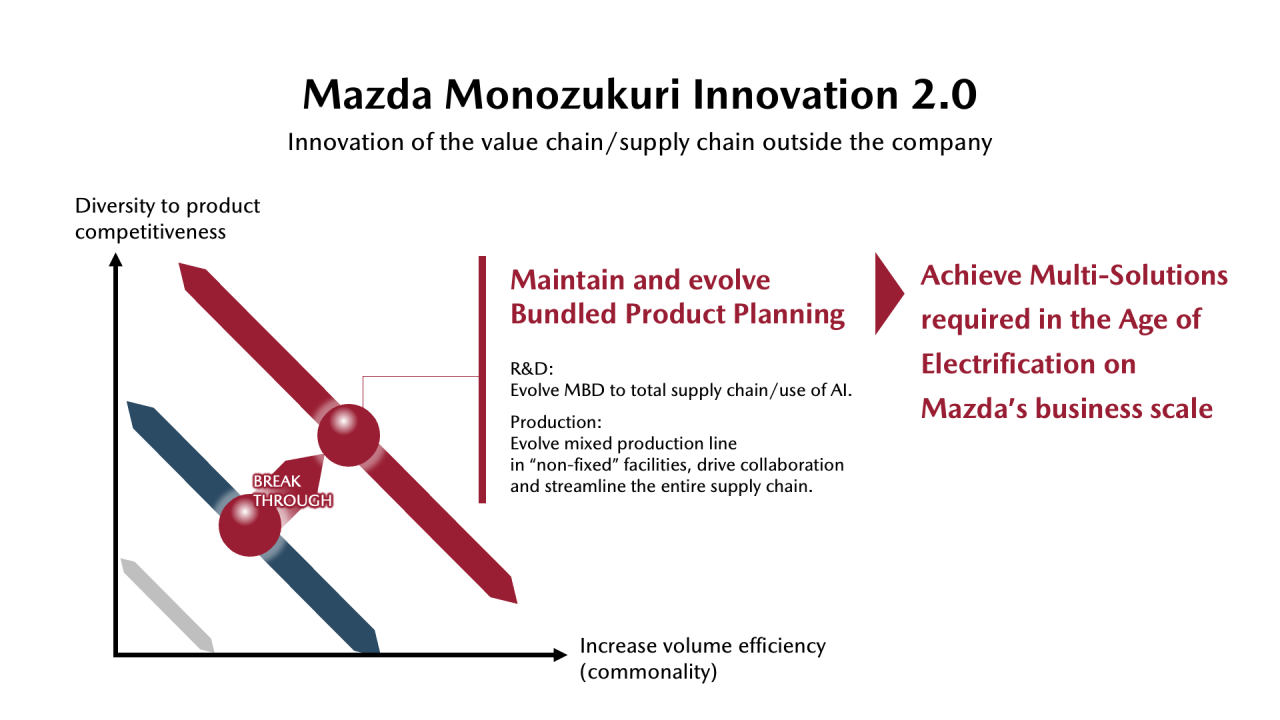
In development, Mazda’s unique Model Based Development (MBD) has been evolved. MBD refers to a development methodology that uses modeling of various characteristics that are reproduced on a computer, designed to streamline the development process. Model Based Development (MBD) in Monozukuri Innovation 1.0 was based on an individual unit, such as combustion and collision. In Monozukuri Innovation 2.0, individual unit-based MBD is upgraded to a Total Vehicle Model, so that the entire vehicle is covered by connecting unit-based models. This enables Mazda to clarify functional and performance targets, as well as identify how to structure models and find ways to control each.
In addition, through co-creation with other entities such as the MBD Promotion Centre (JAMBE), we have extended model-based development throughout the whole supply chain, thus achieving more efficient development.
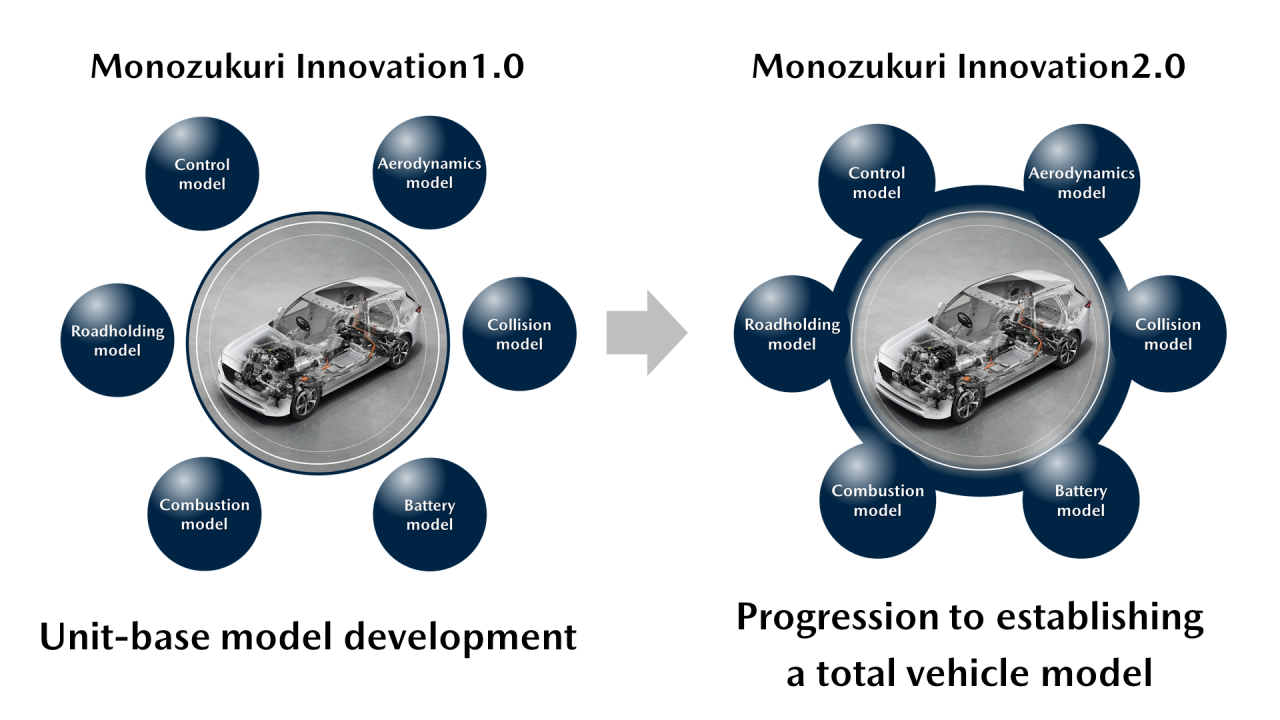
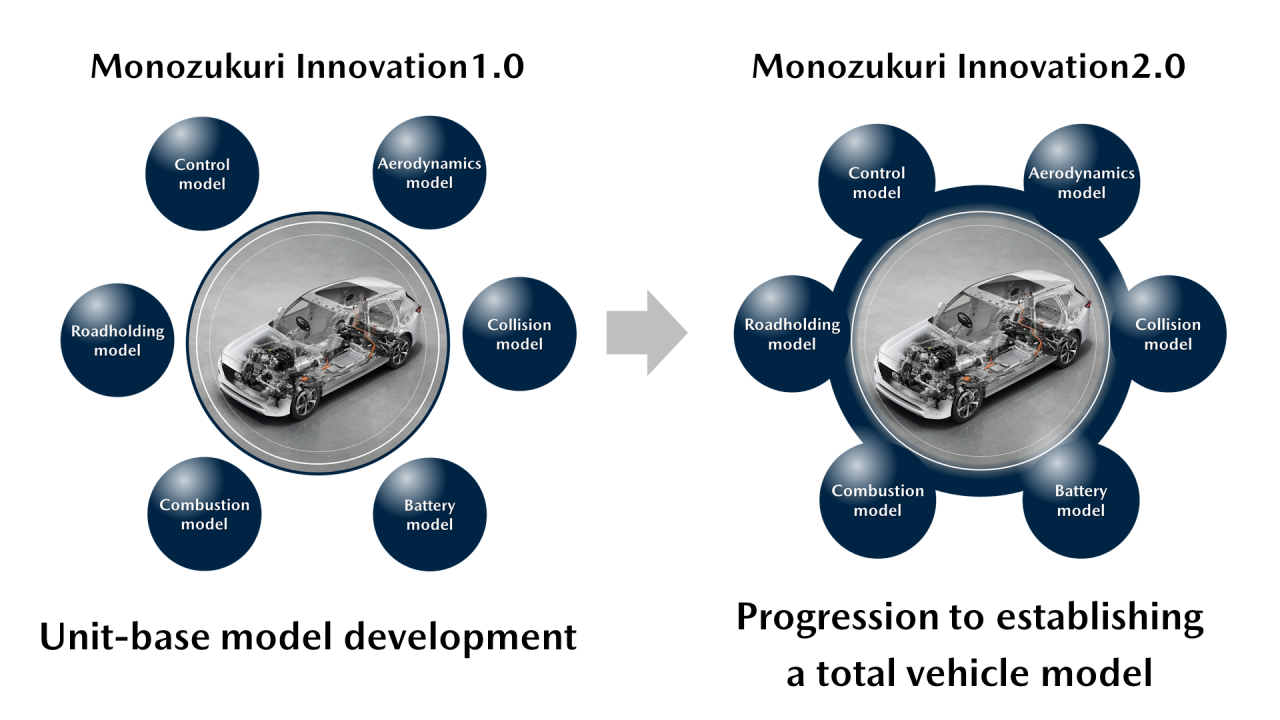
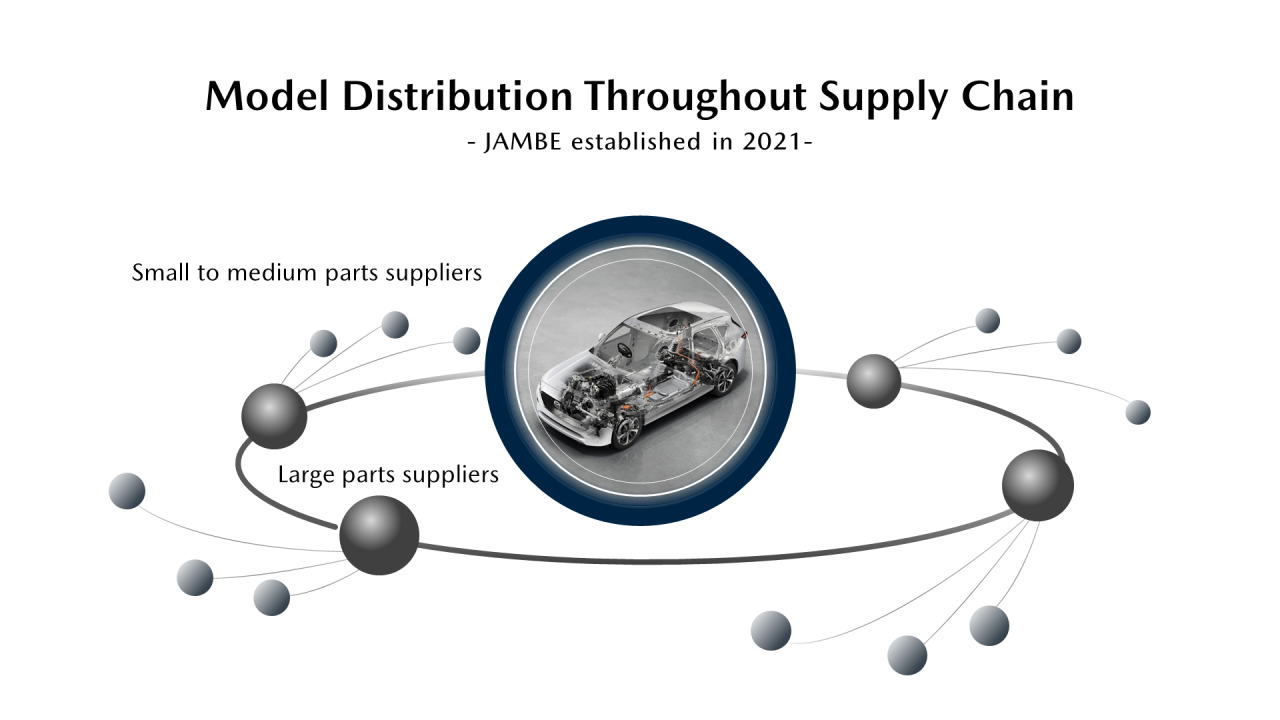
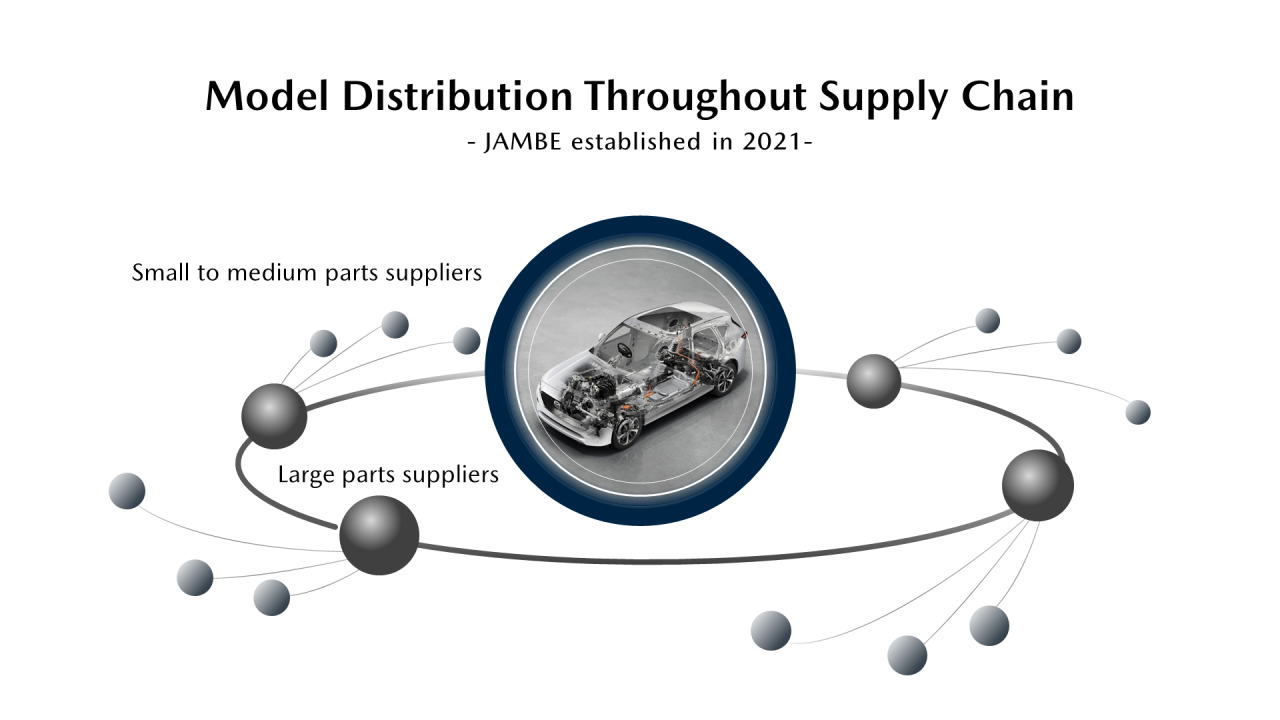
In production, “non-fixed production facilities” established by adding Automatic Guided Vehicle (AGV) to mixed production line, nurtured over the years as Mazda’s strength, were introduced to enable mixed production of Battery EV and ICE models. This is intended to secure flexibility for accommodating demand variations and improve asset efficiency.
Mazda is also driving supply chain structural transformation by optimizing number of parts types by co-creation with our supplier partners to bring the places where these parts are produced closer to the vehicle plants. Taking vehicle control devices and software, both of which are expected to increase in variety with the progression of electrification, as an example, one hardware is used for software programming. Supplier only installs and supplies the software common to carlines, while model-dedicated software is installed in our plant through “Factory OTA” technology, a practical method of wireless communication. This will allow us to flexibly cater to customer’s changing demands and reduce inventory in the supply chain at the same time to quarter.
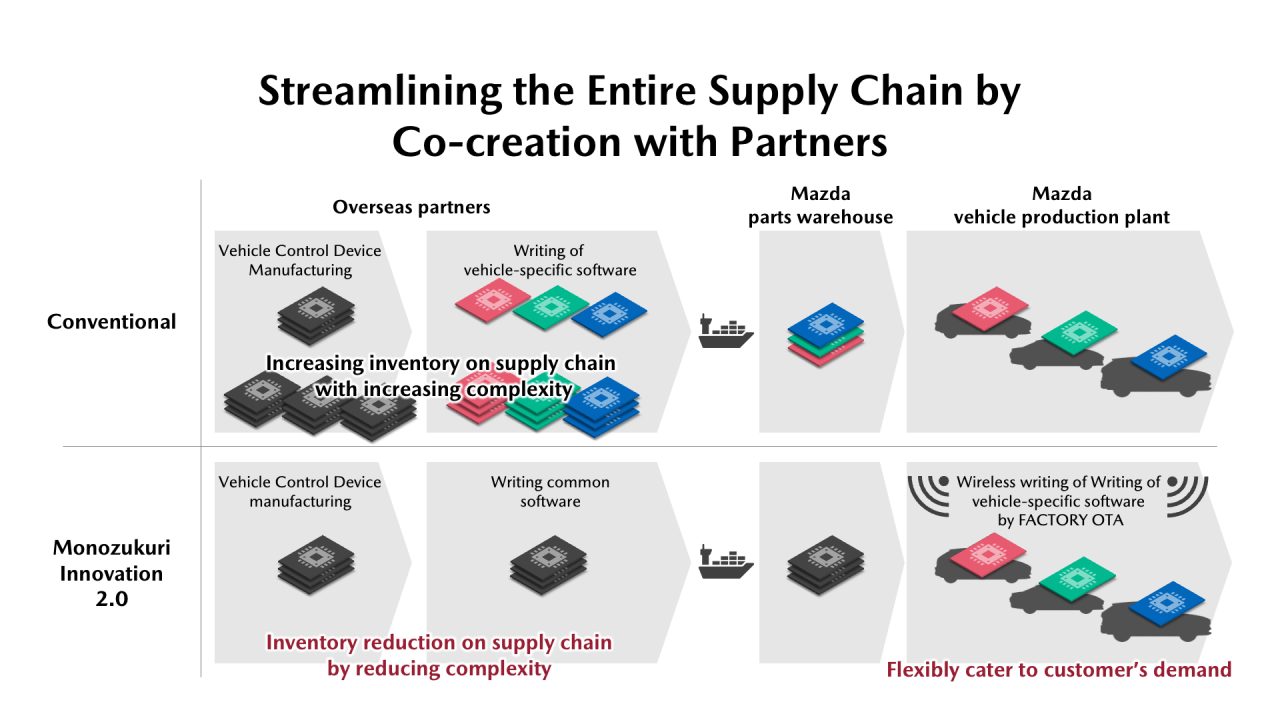
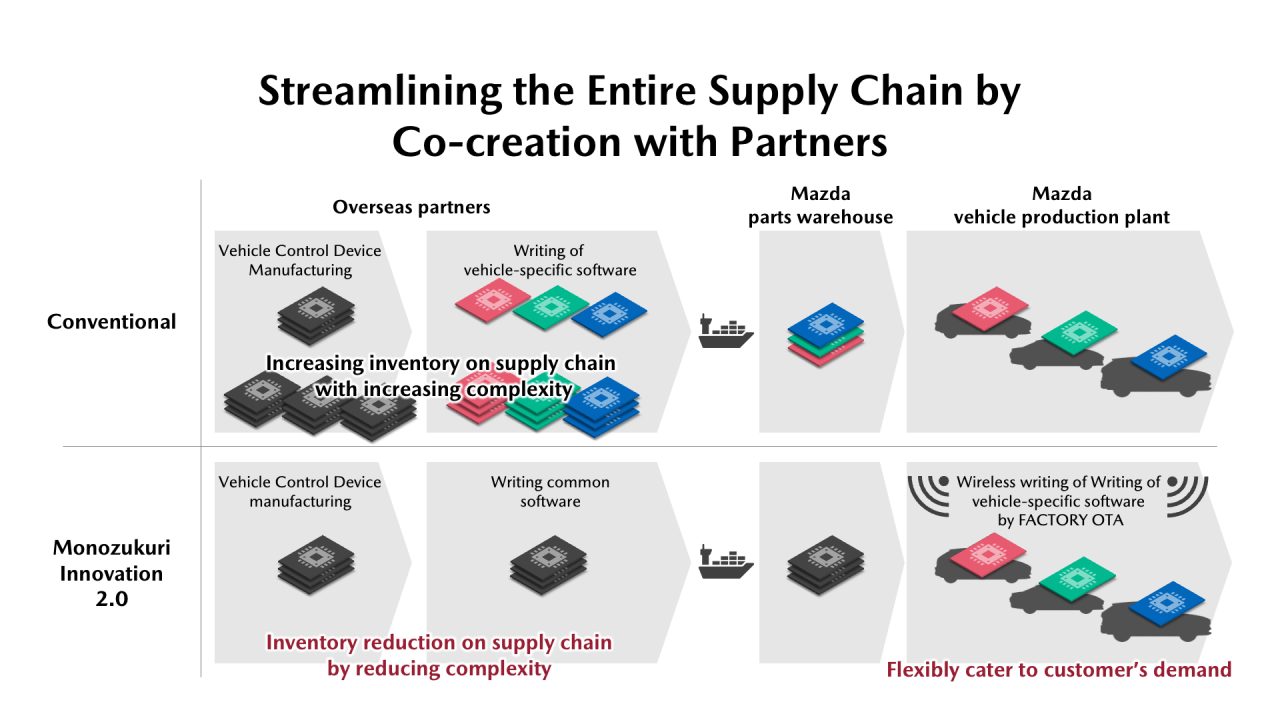
SKYACTIV-Z
In the Age of Electrification, Mazda aspires to be a frontrunner for internal combustion engines. The SKYACTIV-Z 2.5L in-line 4-cylinder gasoline engine, which is currently under development, will be combined with electrification technology to achieve a higher level of driving performance that customers can enjoy, while also meeting the strict emission regulations of Euro 7 in Europe, as well as LEV4 and Tier 4 in North America. It will become a core engine in Mazda’s engine line-up for the Age of Electrification.
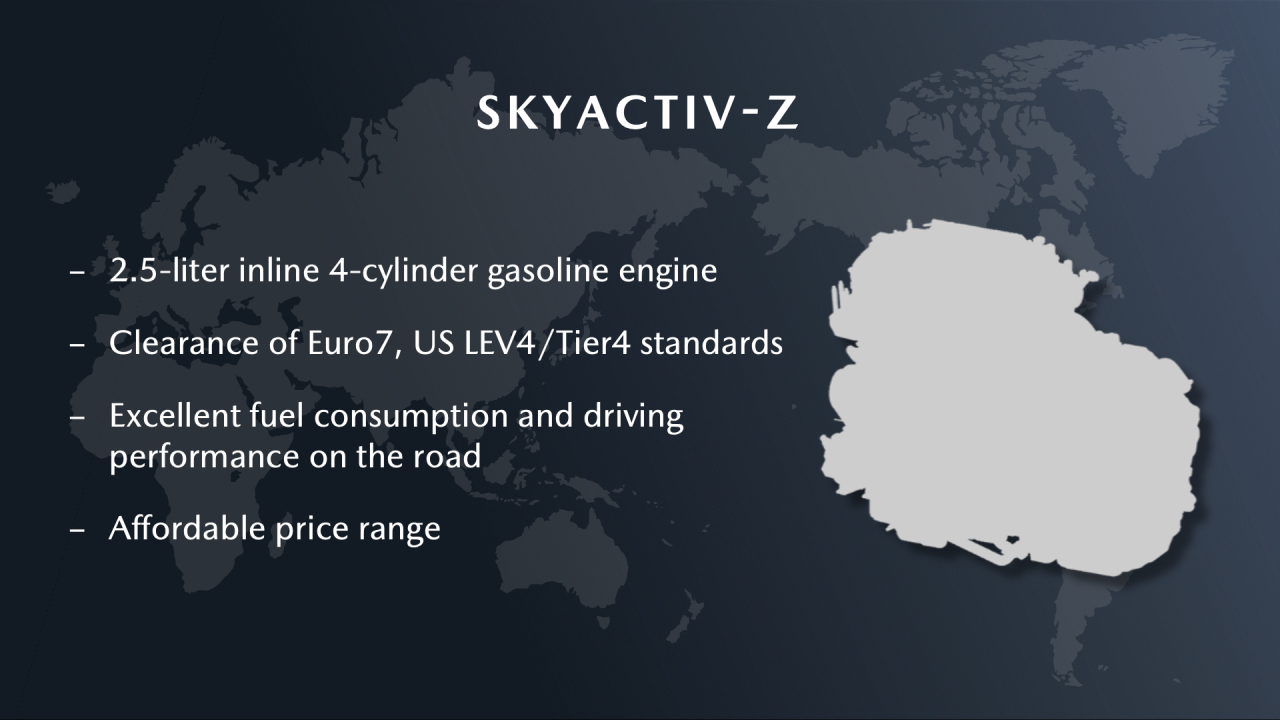
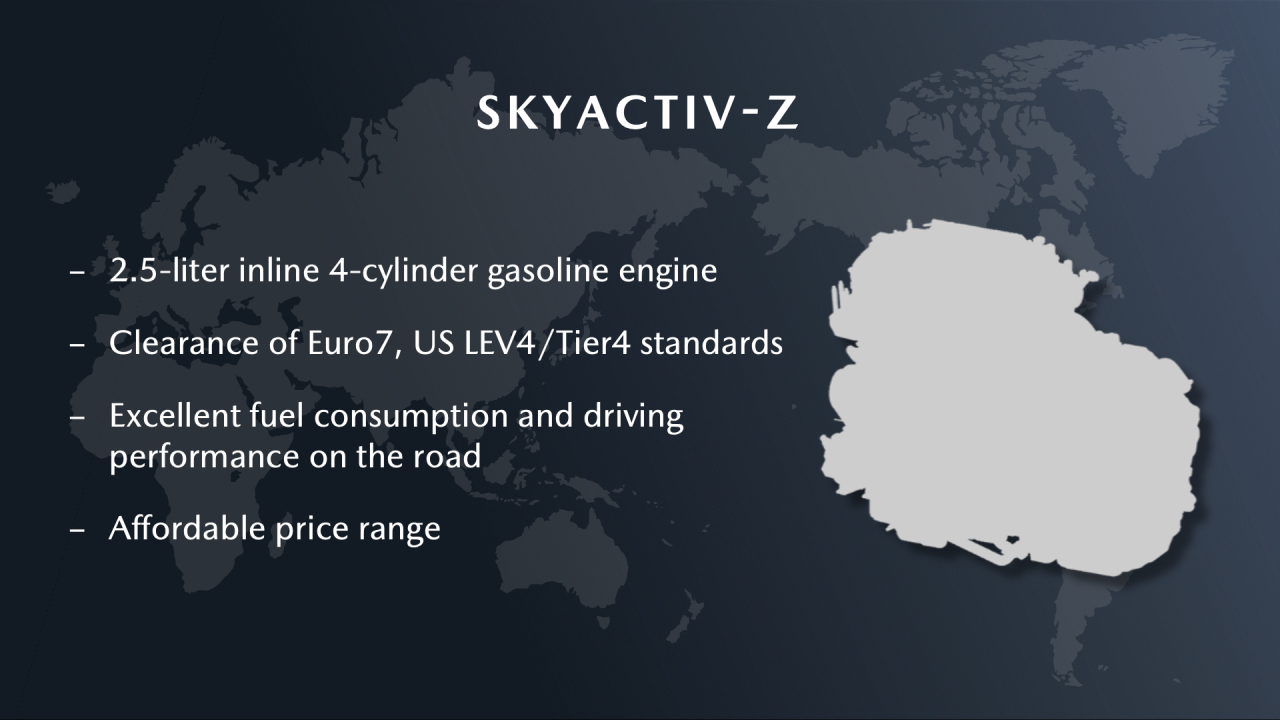
Following the SKYACTIV-G, the SKYACTIV-Z is the final step on the roadmap toward the ideal internal combustion engine. For the SKYACTIV-X commercialized in 2019, use of AI in combustion model substantially accelerated conformity development, and contributed to the world’s first lean compression ignition combustion; SPCCI Combustion. By expanding the area of SPCCI combustion and accumulating combustion technology for reaching the ultimate combustion threshold, the SKYACTIV-Z will be the engine that balances excellent fuel consumption performance and driving performance.
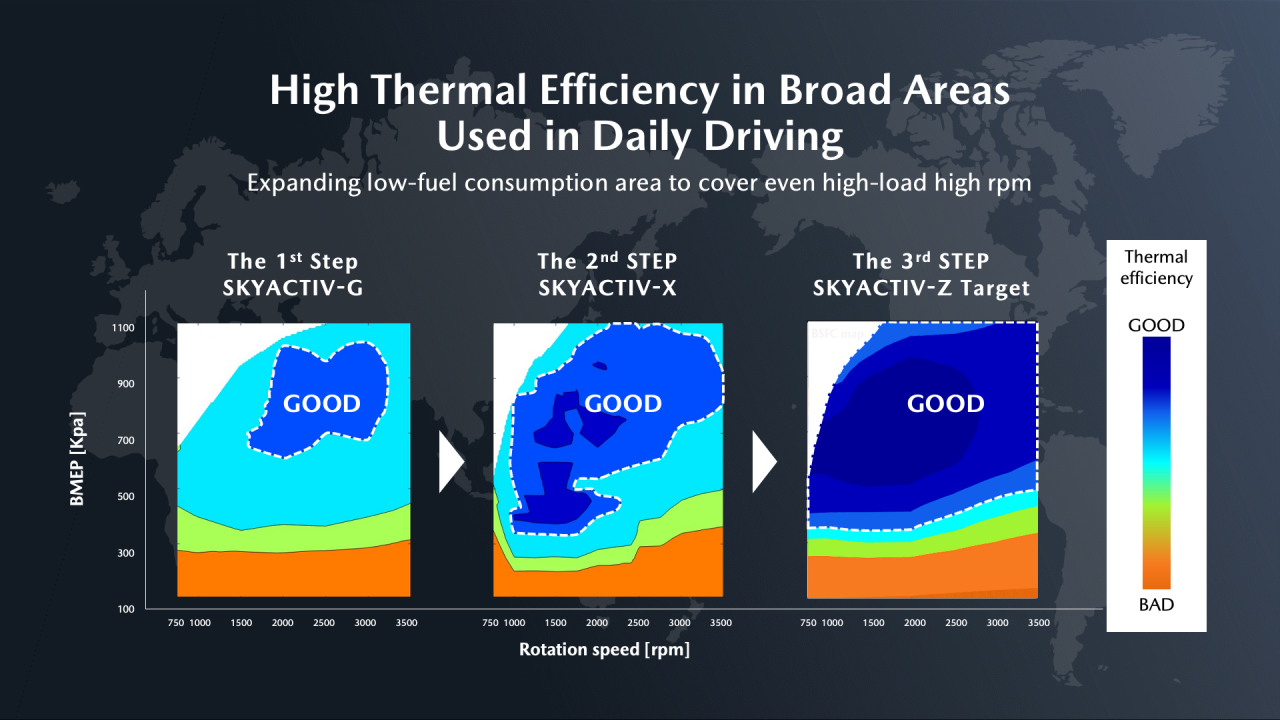
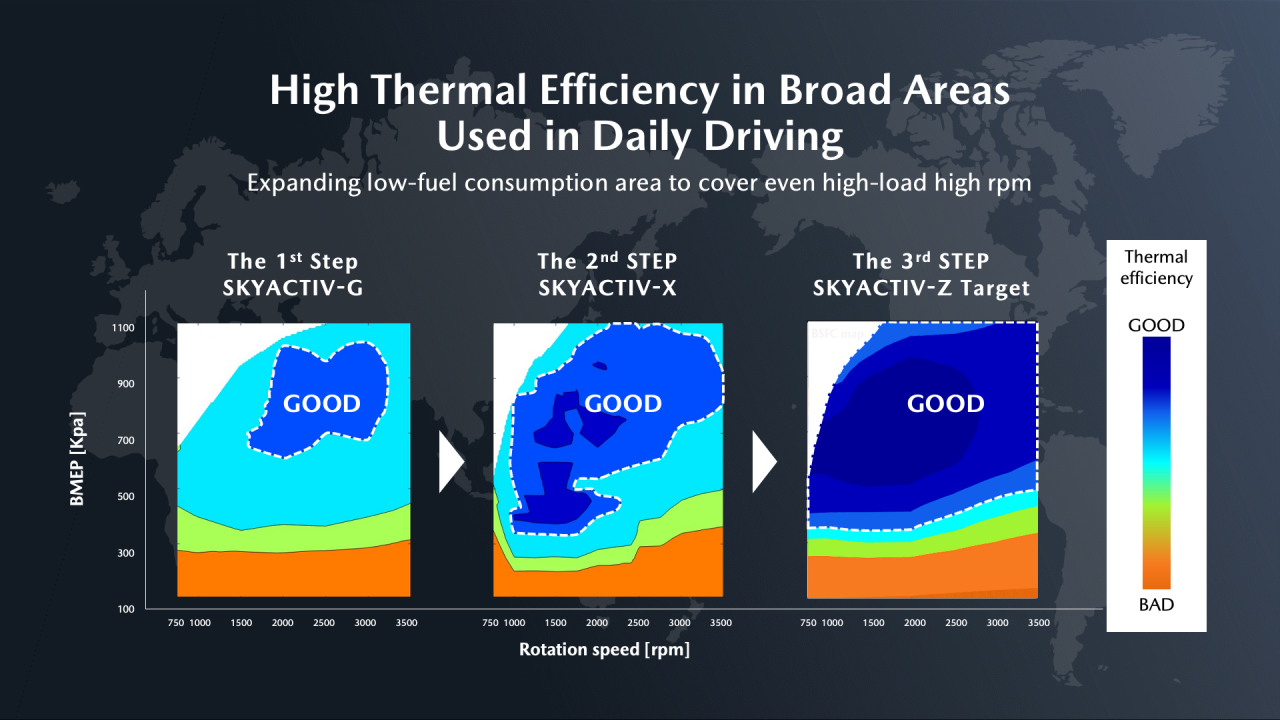
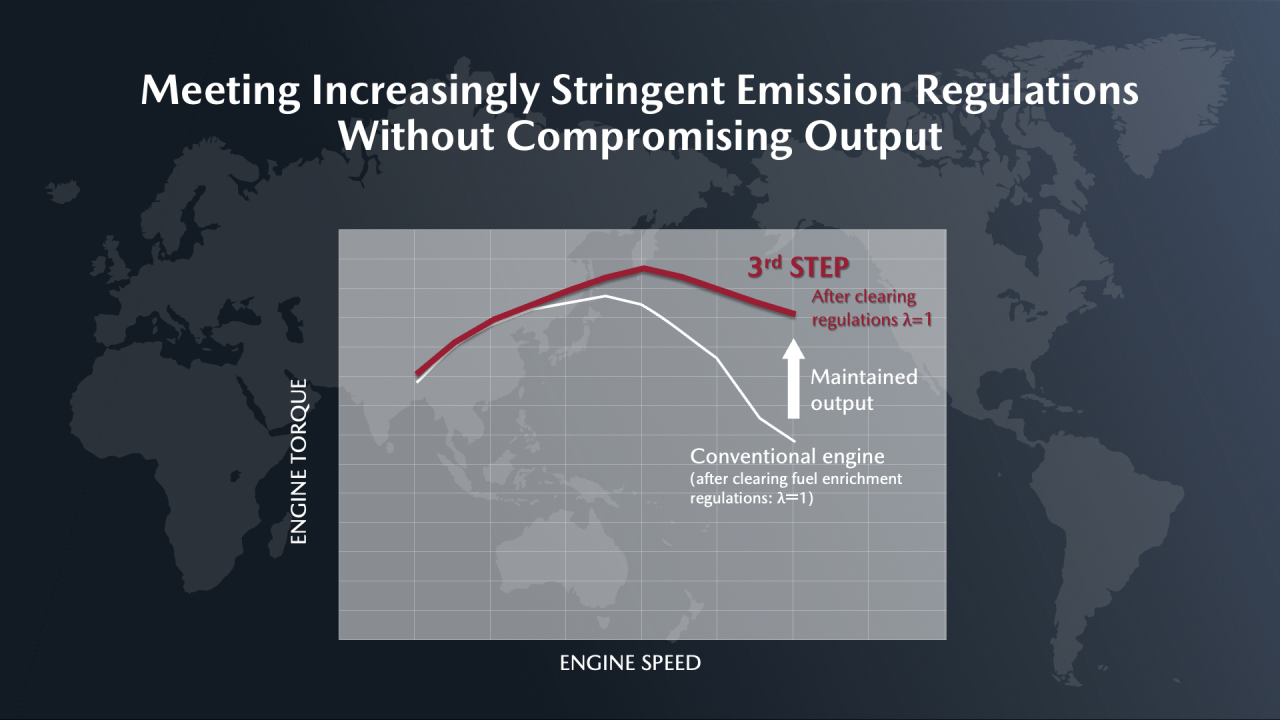
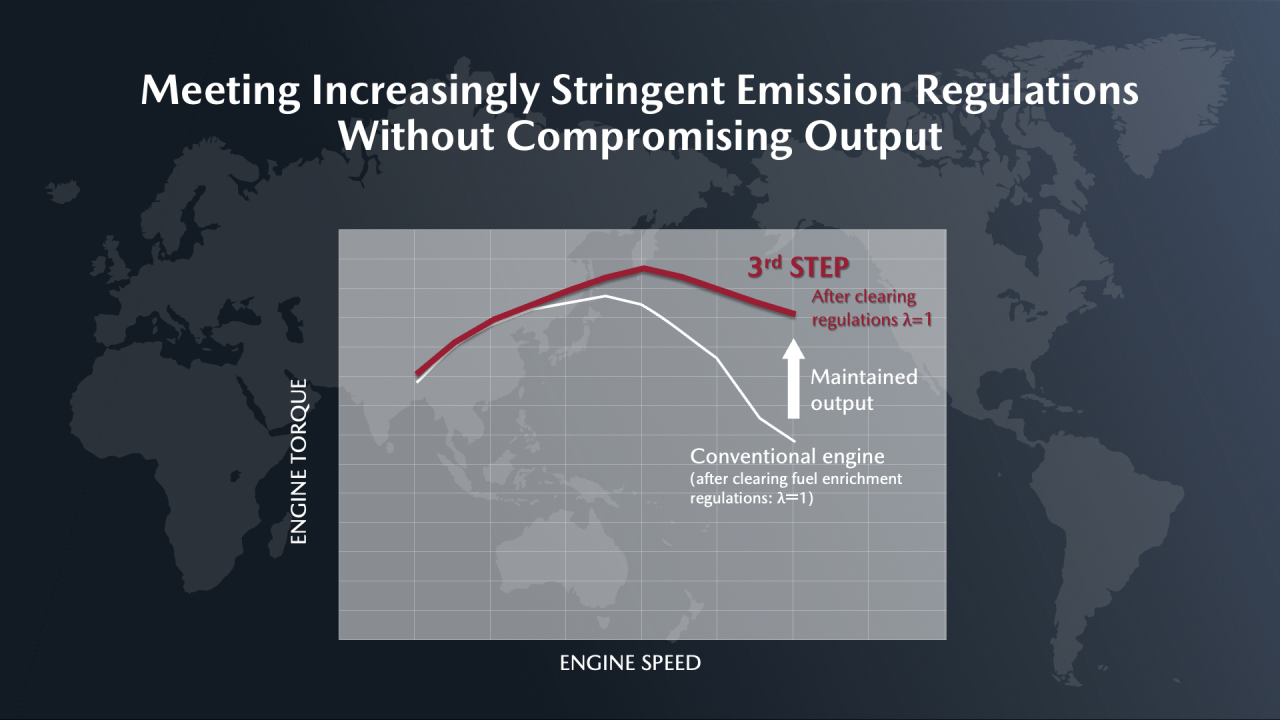
The SKYACTIV-Z will be combined with Mazda’s unique hybrid system and scheduled to be introduced to the next-generation MAZDA CX-5 launched by the end of 2027.
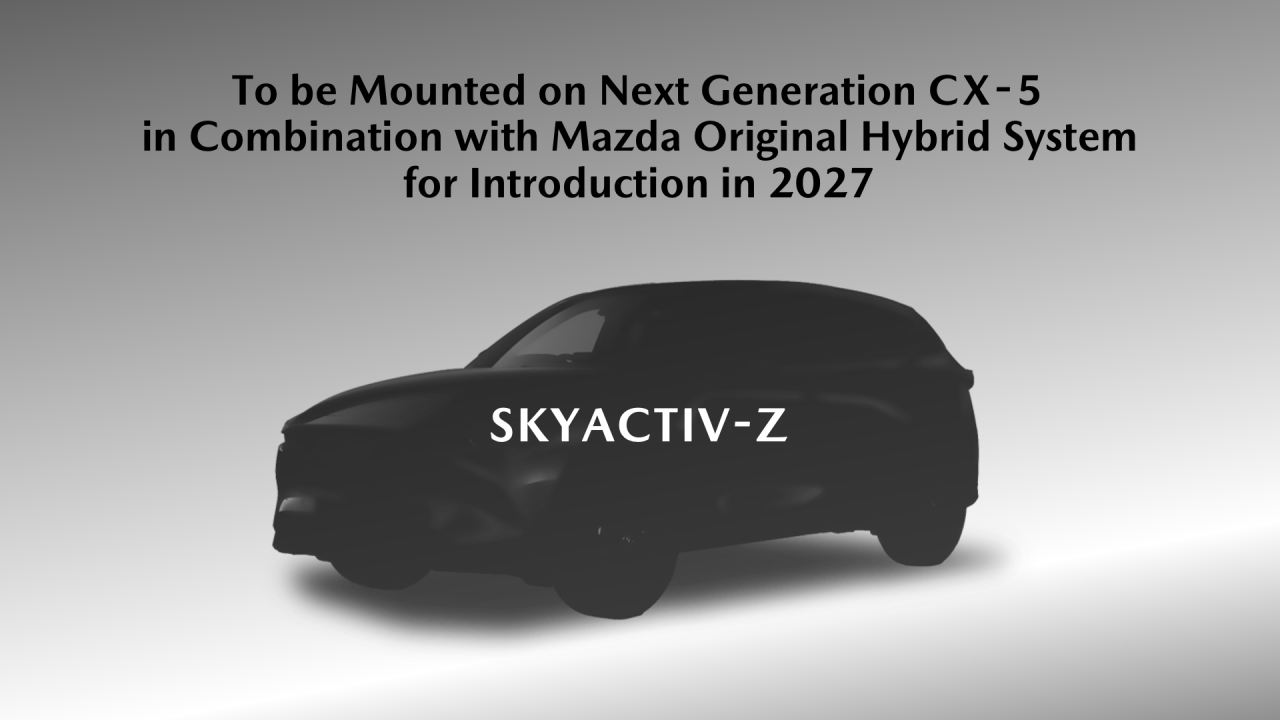
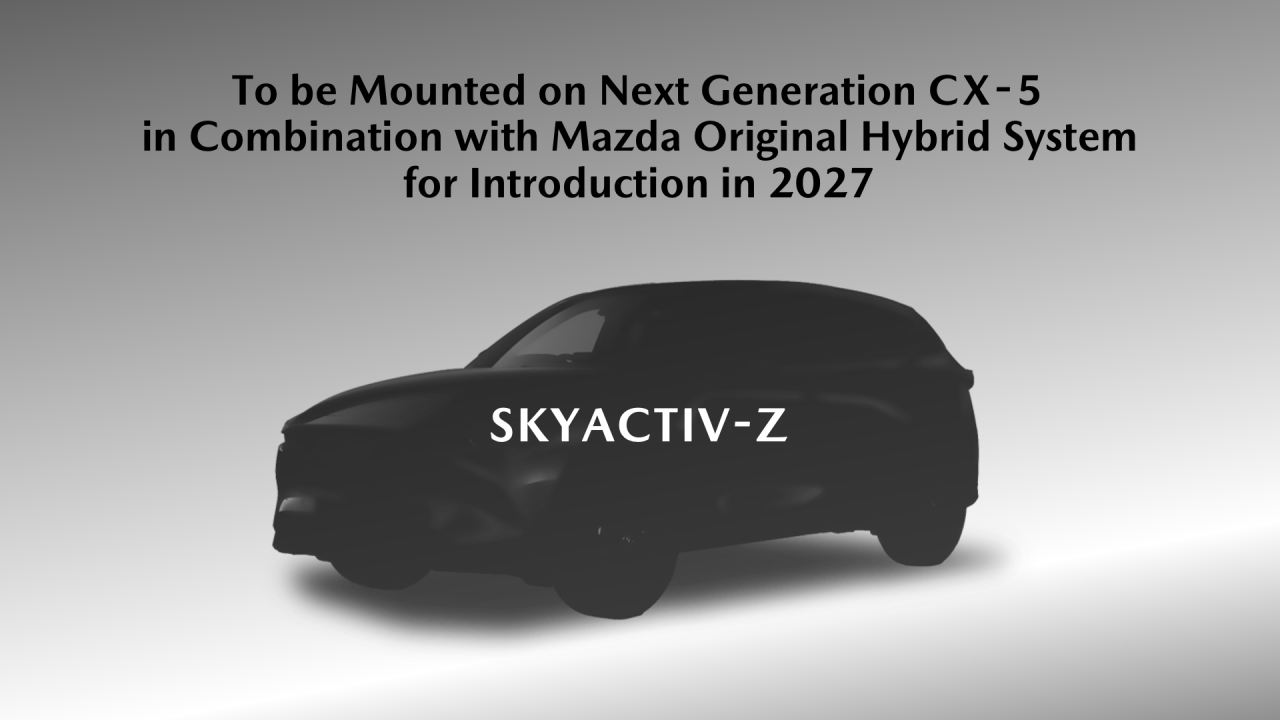
The combustion improvement technologies that were accumulated before and during the development of SKYACTIV-Z will be applied to the inline 6-cylinder engines of Mazda’s large architecture product range, and will also serve as a roadmap for meeting the strict emission regulations for rotary engines. Based on this, in the future, the number of engine units as hardware, including the SKYACTIV-Z, will be consolidated to less than half, and the control software will also be reduced to two-thirds.
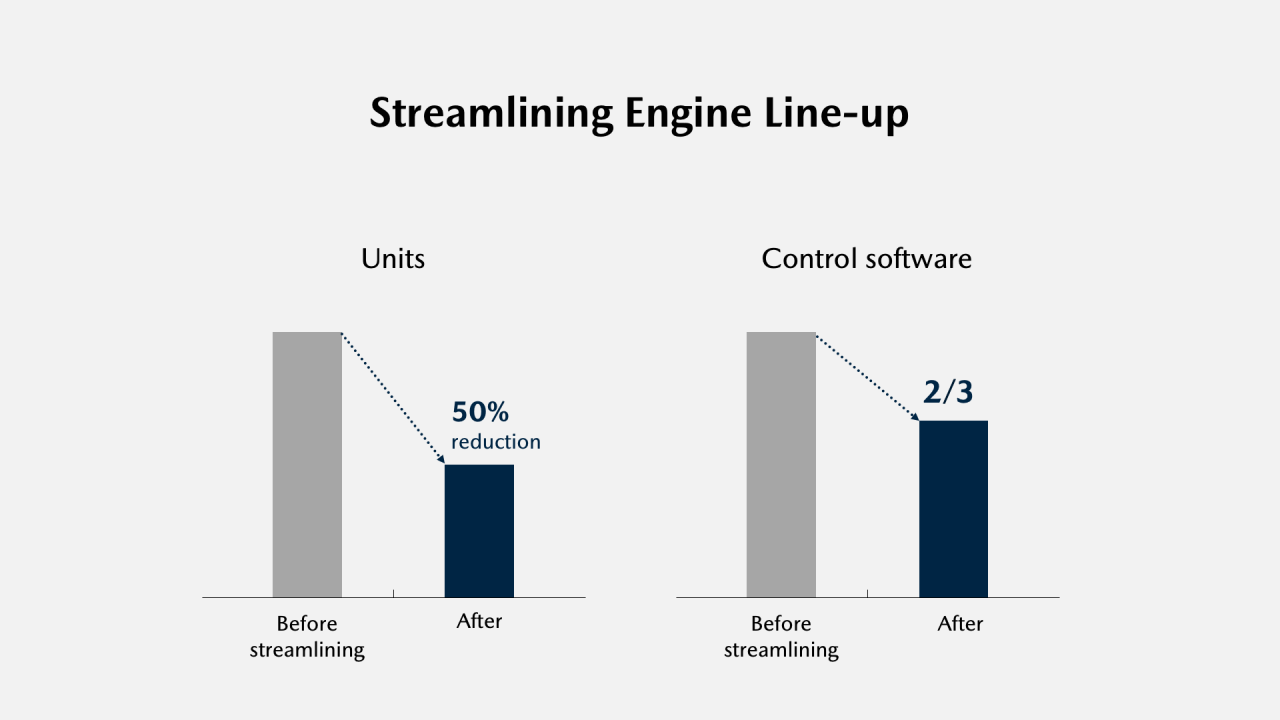
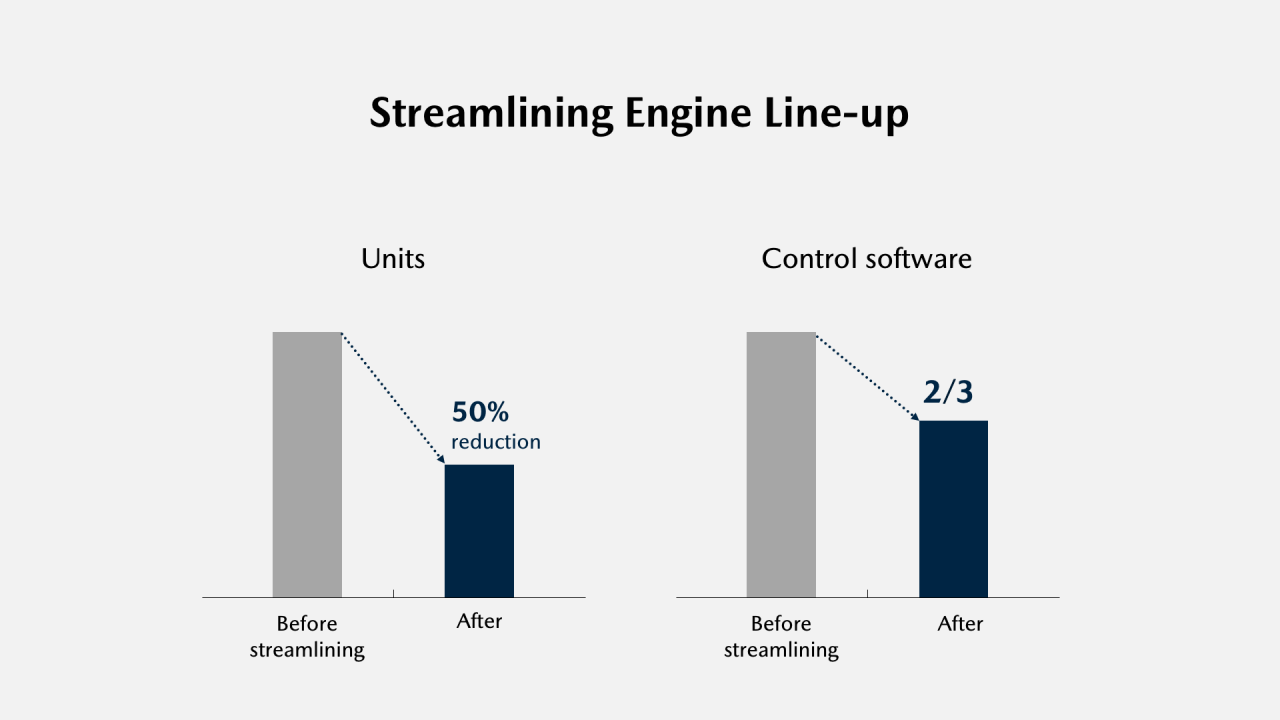
BATTERY EV
Mazda is taking full advantage of its Lean Asset Strategy and Monozukuri Innovation 2.0 for its Battery EV to balance Mazda uniqueness such as Mazda-unique design, Jinba Ittai responsive driving performance, and excellent craftsmanship, with high-efficiency development in a higher dimension.
To keep pace with the ongoing evolution of battery technologies, a self-developed EV-dedicated platform is designed to flexibly accommodate different battery types and produce model derivatives.
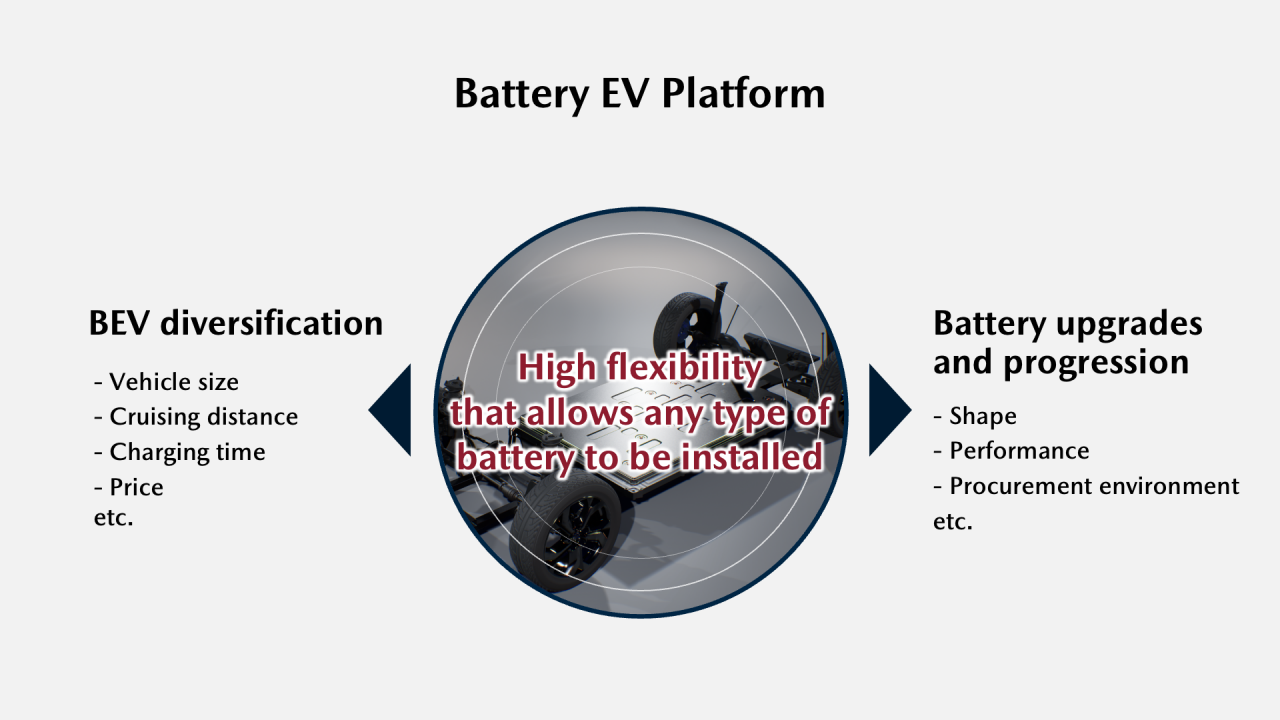
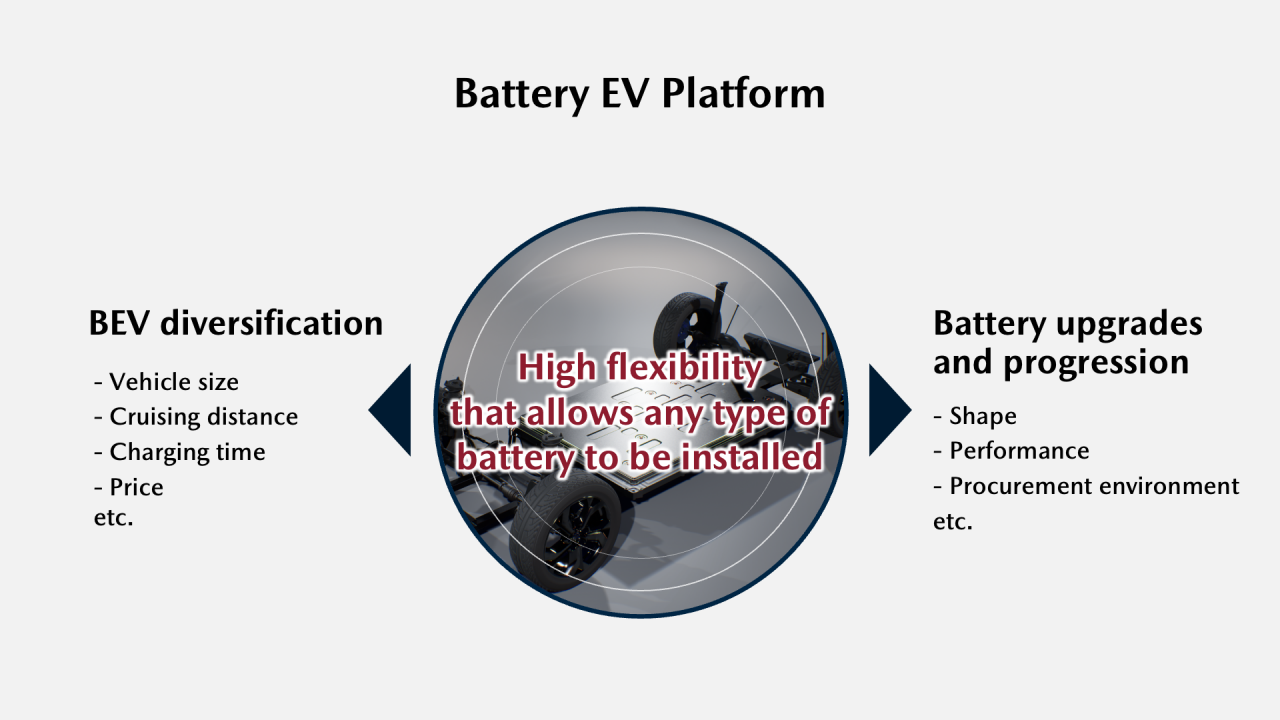
Mazda is developing Battery EV as a vehicle that is fun to drive, delivering Jinba Ittai driving feel to customers. Using integrated control technologies for the entire vehicle, developed through a progression to Monozukuri Innovation 2.0, Mazda is set to deliver stable driving, and driving experience that makes drivers feel that their vehicle quickly responds to their will.
*A prototype vehicle with next-generation battery technology (The exterior is that of an existing model)
ROADMAP FOR THE ELECTRIFICATION TRANSITION
The SKYACTIV-Z will be a core engine for the age of electrification, and will be installed in the next-generation MAZDA CX-5 in combination with Mazda’s unique hybrid system by the end of 2027. The combustion improvement technology of the SKYACTIV-Z will be deployed to the inline 6-cylinder engines of the large architecture products. In addition, it will also be used in the roadmap for the development of rotary engine emissions. Applying the element technologies of the hybrid system to our large architecture products will also be considered.
A battery EV model, which will use Mazda's first dedicated EV platform, is planned for launch in 2027. By utilizing a dedicated EV platform, Mazda's unique Jinba Ittai driving experience will come alive with a high degree of commonality and low investment. Development of a plug-in hybrid derivative will be considered. In addition, following the MAZDA EZ-6, which is manufactured by the joint venture Changan Mazda Automobile, with the development of the second crossover SUV is progressing smoothly, and the third and fourth models being considered.
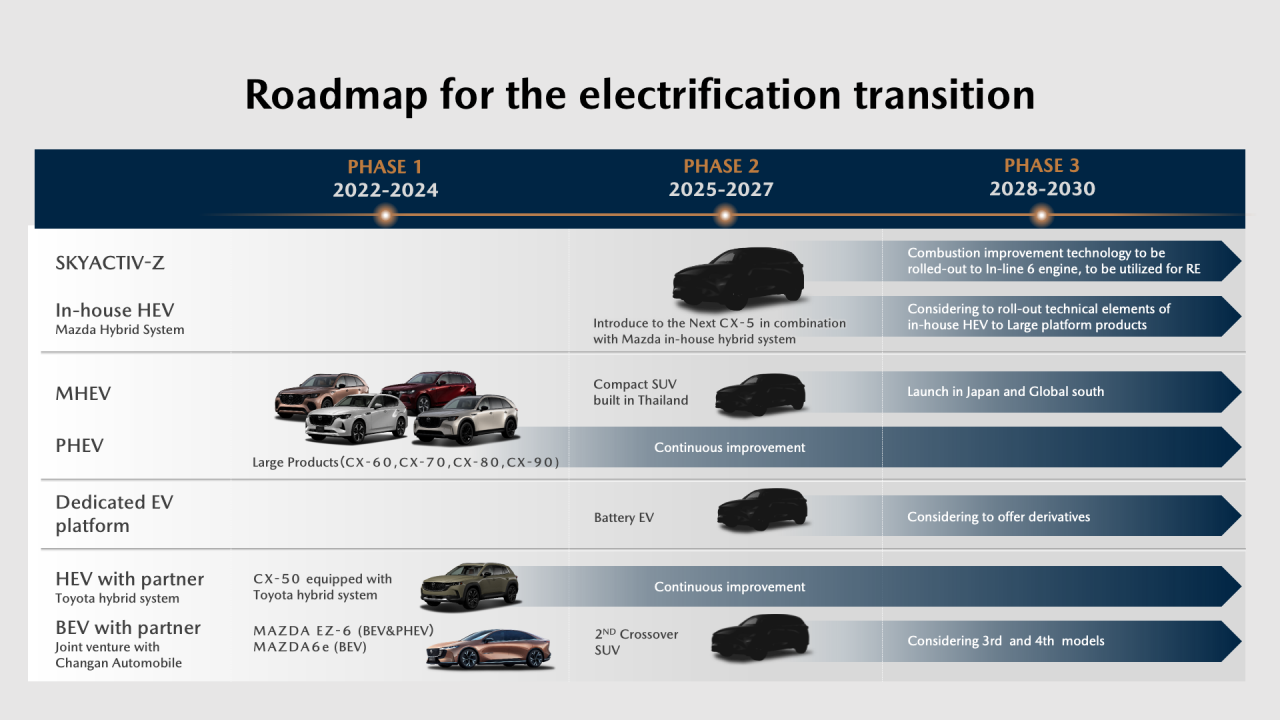
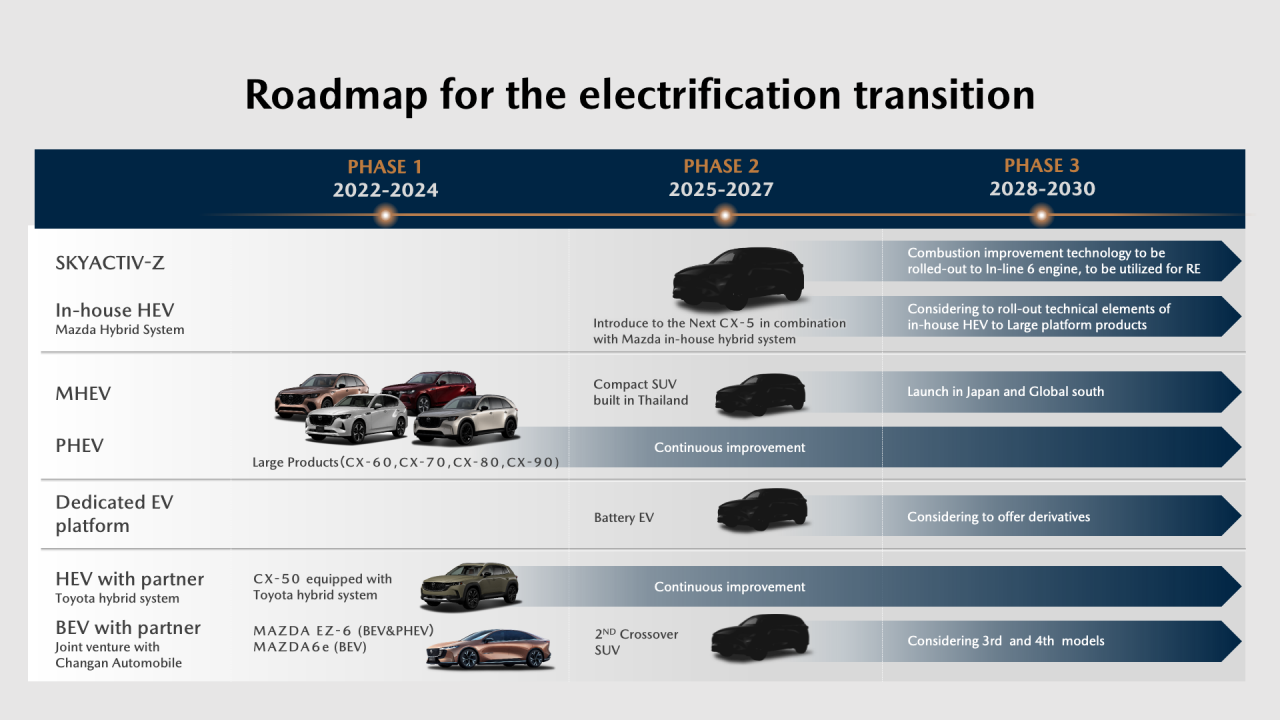